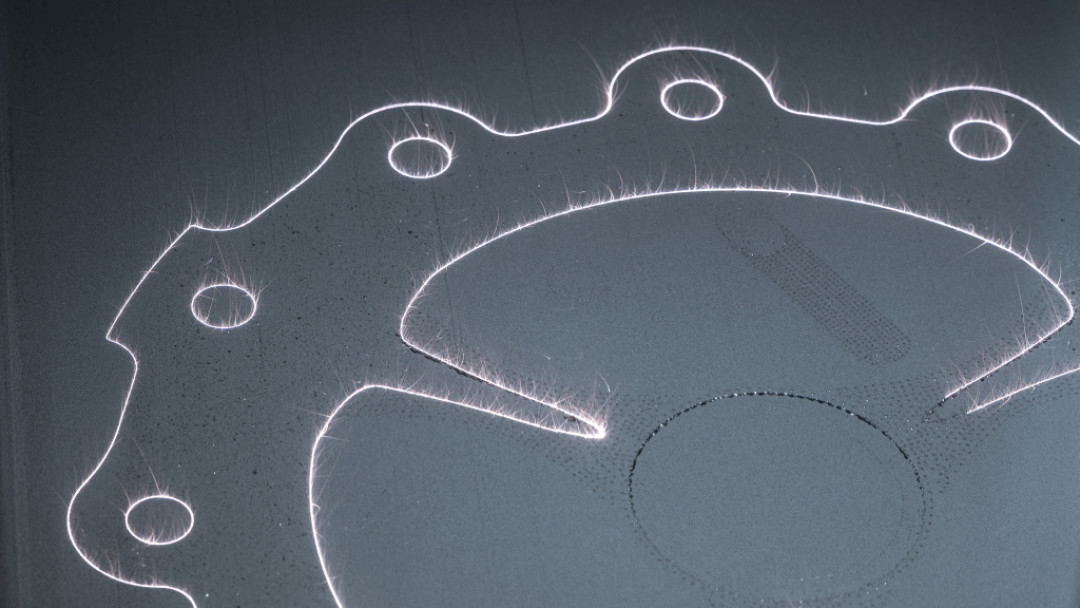
Fraunhofer IWS Installs Europe’s Unique Industrial 3D Printer “SpreeTec next”: Powder Bed-Based Additive Laser
The Fraunhofer Institute for Material and Beam Technology IWS in Dresden will install a Europe-wide unique industrial 3D printer. The Additive Manufacturing system from manufacturer Farsoon is based on selective laser beam melting in a powder bed. It can produce substantial components with complex geometries from aluminum, titanium, nickel, iron, copper, and other metallic powders layer by layer.
Fraunhofer IWS scientists are directing their research and development work with the manufacturing facility, such as combustion chambers for hydrogen energy systems, blade wheel enclosures for turbines, and other complex machine components or tools. With their help, together with the Brandenburg University of Technology Cottbus- Senftenberg (BTU) in the joint project “SpreeTec neXt”, they want to establish new manufacturing processes and value chains for the post-coal era in Lusatia, for instance. Entirely new business models for repairing spare parts that are difficult to obtain for agriculture, energy technology, or industry may also be foreseeable.
Unique Selling Propositions for Regional Small and Medium-Sized Businesses
“With such system technology, the East German SMEs can develop special unique selling propositions with the help of Fraunhofer IWS,” emphasizes institute director Prof. Christoph Leyens. “Especially in the transformation region of Lusatia, projects like ‘SpreeTec neXt’ give new impulses to the regional economy.” It is true that some companies already use 3D printers. However, these devices are usually limited in their capabilities. For example, they only specialize in plastic prototypes, can just produce comparatively small metallic components, or, although significant, tend to produce less complex shaped components using other manufacturing processes such as buildup welding. However, modern 3D printers like the one at Fraunhofer IWS reshuffle the cards: the new AM system can generate components that measure up to 62 by 62 by 110 centimeters.
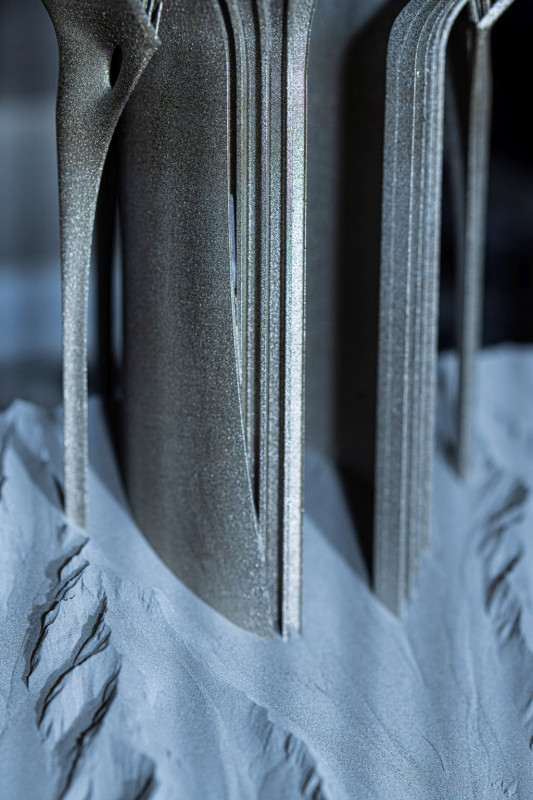
“This system thus offers completely new possibilities to additively manufacture even huge components with complex geometry in high quality,” explains Dr. Lukas Stepien, who heads the Powder Bed Processes and Printing Group at Fraunhofer IWS. “Thus, it opens up application opportunities for industrial 3D printing in even more industries and applications.”
For example, decentralized Additive Manufacturing (AM) is conceivable where new components and tools for small batch sizes are permanently needed or replacement components are challenging to obtain—this interests automotive manufacturing, aerospace, the energy plant industry, and toolmaking, for instance. In the future, such large-scale AM systems may also facilitate the rapid procurement of spare parts for high-quality agricultural machinery in the agricultural sector.
New Innovation Center also to Strengthen Regional Structural Change
During “SpreeTec neXt,” the project partners strive to establish an innovation center in the region by 2029 that will strengthen regional structural change. To this end, BTU and Fraunhofer are collaborating in Additive Manufacturing. Fraunhofer IWS contributes its unique expertise in this particular area, in process development, and in materials and component analysis. The BTU is primarily dedicated to basic research for AM processes. The plan is to permanently establish a joint Fraunhofer and BTU laboratory in Lusatia to support sustainable economic development. The team will then advise small and medium-sized companies from the transformation region on the use of advanced technologies related to Additive Manufacturing, provide further training for employees of such companies, and support the growth of an AM cluster in Lusatia. The German Federal Ministry of Education and Research (BMBF) will fund these specific subtasks of “SpreeTec neXt” with five million euros each.
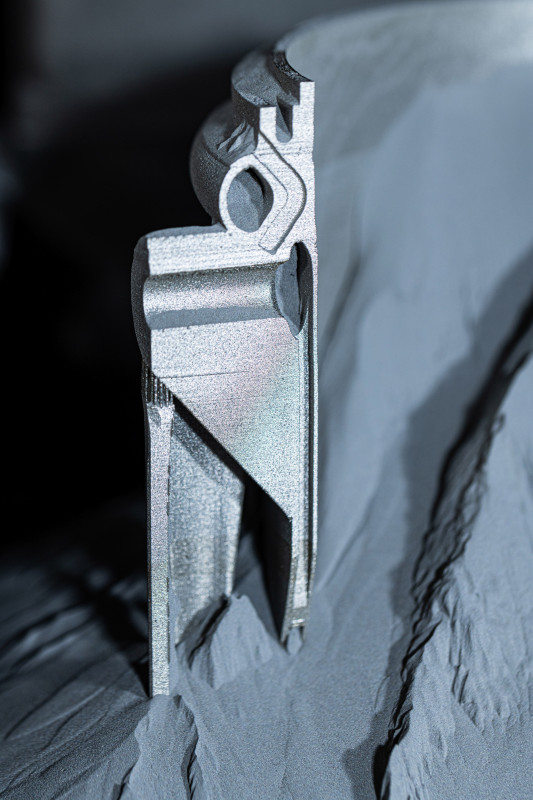
Fraunhofer IWS and its partner Farsoon will offer the first insights into the resulting possibilities at the international manufacturing trade show “formnext” from November 7 to 10, 2023, in Frankfurt am Main.
How does Additive Manufacturing Work in a Powder Bed?
In laser-based Additive Manufacturing in a powder bed, a laser beam melts fine metal particles in a gas environment. From this melt, the system creates the desired component layer by layer according to a computer model. This way, components of titanium, copper, and other metals or their alloys can also be generated.
What is “SpreeTec neXt”?
The joint project “New manufacturing technologies for components and systems in decentralized energy technology” (SpreeTec neXt) aims to bring new resource-saving manufacturing technologies for components and systems in energy generation, conversion, and storage to practical maturity. These can include, for example, hydrogen-powered turbines and fuel cells, heat exchangers, or hybrid photovoltaic and solar thermal systems. New materials, digitization approaches, and cycle principles for these applications are also on the project agenda.
The Brandenburg University of Technology Cottbus-Senftenberg (BTU) has taken over the lead management. The Fraunhofer Institute for Applied Polymer Research IAP from Potsdam and the Fraunhofer Institute for Material and Beam Technology IWS from Dresden are partners. The German Federal Ministry of Education and Research (BMBF) funds the seven-year project with 52.44 million euros.
(Source: Press Release of Fraunhofer-Institut for Material and Beam Technology IWS)