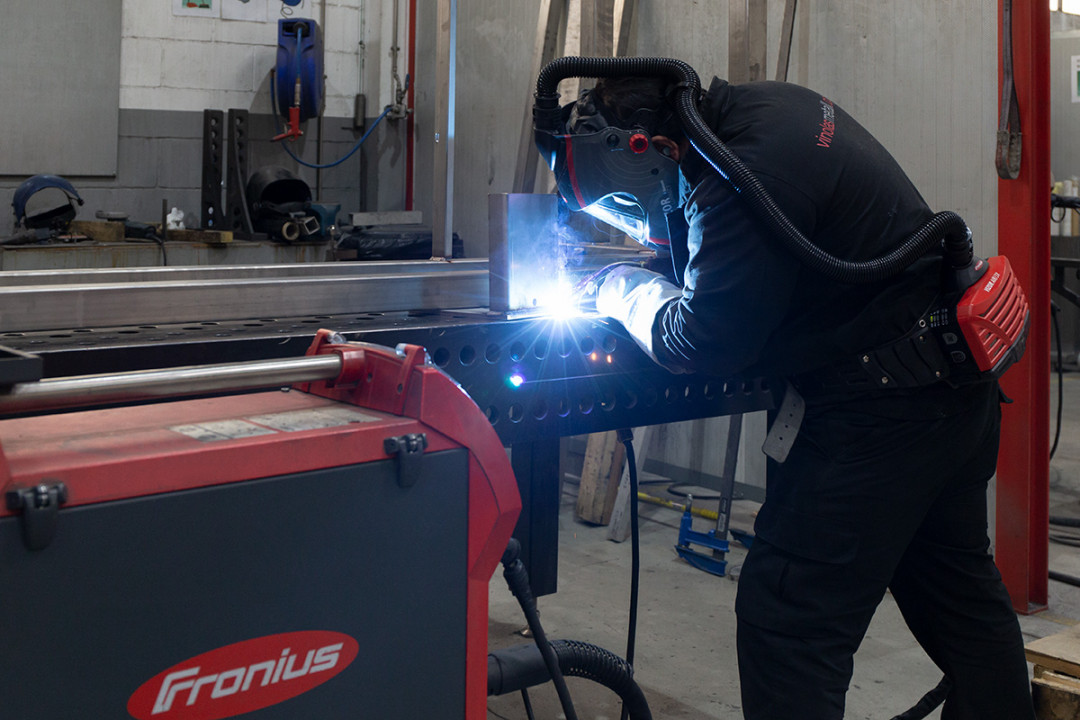
Gearing up for Industry 5.0 with new welding solutions
Viñolas Metall is a family business specializing in the construction of metal components, sheet metal processing, and boiler making. As part of their latest innovation measures, a CMT robotic welding cell was introduced in combination with a TPS 400i power source for the series production of identical parts. At the same time, the iWave Pro series – the new generation of Fronius multiprocess welding machines – is used for certain applications.
Josep Viñolas founded Viñolas Metall in 1968 in Cornellà del Terri, Spain, and the company has been producing metal constructions for companies and private consumers ever since. Years later, his son David Viñolas joined the company and invested in new machinery and technologies for the export business and to optimize project workflows through computerization. A 4,000 m2 production site in Banyoles was recently opened to complement the existing 800 m2 assembly workshop in Cornellà del Terri. In addition, Viñolas Metall has been certified to ISO 3834-2 by the Fronius Welding Academy. The company has a diverse range of customers from different industries, including winemaking, water treatment, swimming pool accessories, mechanical engineering, plant construction, toolmaking, power plant construction, and railway construction.
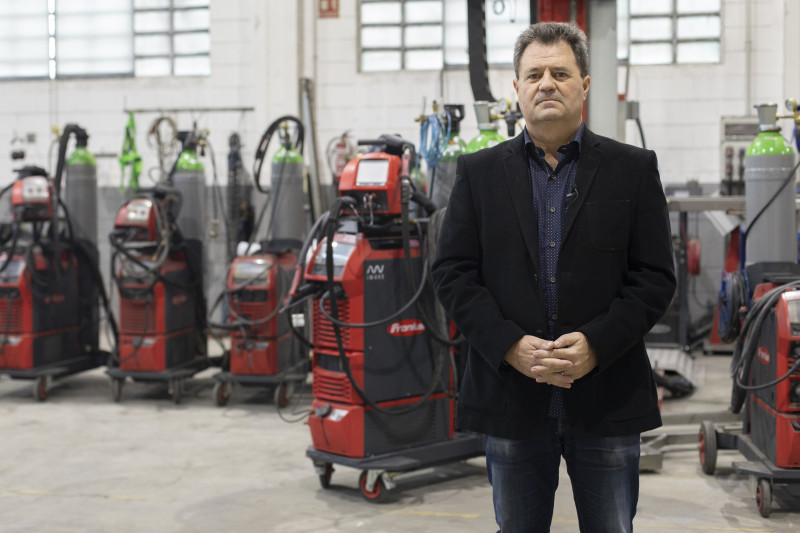
Current situation and new challenges
Welding currently accounts for 70 to 80 per cent of production times. Carbon steel, stainless steel (304, 316, duplex, and super duplex), aluminium, and COR-TEN® are the most common materials processed. It is mainly smaller components that are joined, but also large and heavy components. Sheet thicknesses range from 2 to 40 mm. Welding is carried out in the PA (flat), PB (horizontal), and PC (horizontal) positions. Out-of-position welding on vertical beams and pipes is performed in the PF (vertical up position) and PG (vertical down position) positions. The most frequently used processes are TIG and MIG/MAG for manual tasks, as well as the ArcTig keyhole welding process for automated applications. Orbital welding systems are also used, whereby the welding torch rotates around the component during joining.
As they specialize in technically demanding, complex metal structures, Viñolas Metall faced two new challenges. The first was finding a solution for creating high-quality, reproducible welds for series production where industry specifications and welding standards had to be taken into account. The components produced are exposed to high loads and used in a highly corrosive environment – for example, in plant construction. The second requirement focused on welding autonomy and system optimization. The desired system should be able to switch between two welding processes (TIG and MIG/MAG) independently and without sacrificing the weld quality, all in the course of a quick process change.
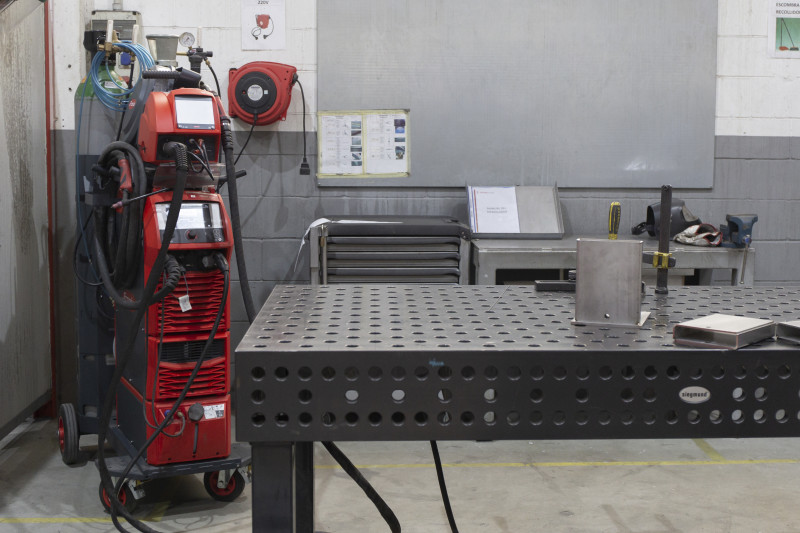
The solution: Robotic welding cell with TPS 400i CMT
“When we need to weld identical parts with the highest weld quality, we turn to Fronius, as they always have the solution we’re looking for,” says David Viñolas, managing director of Viñolas Metall. One specific challenge for Viñolas is welding beams for swimming pool roofs from austenitic chrome-nickel steels 304 and 316. The welding solution consists of a robotic welding cell equipped with a TPS 400i CMT welding machine, a hollow arm welding robot, and an H reverser, which has two vertical turntables on a horizontal axis on both sides. Custom-made clamping devices are mounted between the turntables, each of which can accommodate four of the stainless steel beams.
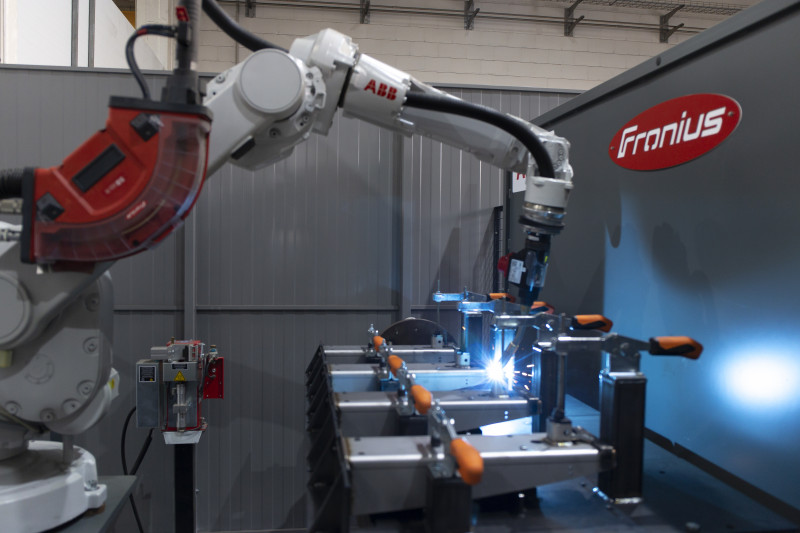
Once one side of the H reverser is loaded with four steel beams, they are turned into the welding cell and joined in a single cycle. Meanwhile, on the other side, the finished welded components can be removed and four new ones positioned, saving valuable cycle time. As soon as teaching of the system is complete, the sequence program together with axial movements is specified and the weld quality ensured. The component handling itself can be carried out by trained operators who do not have to be experienced welding specialists – a particular advantage in times of skills shortages.
“We want our best welders to work on large projects with high added value, while smaller series parts can be welded with the robotic welding cell,” explains mechatronics engineer Matheus Borborema. The Cold Metal Transfer (CMT) process used in the welding cell is characterized by its minimal heat input, which reduces the heat-affected zone and thus the deformation of the base material. At the same time, it impresses with its extremely high arc stability. CMT enables higher welding speeds with low spattering, minimizing uneconomical rework and costs for consumables.
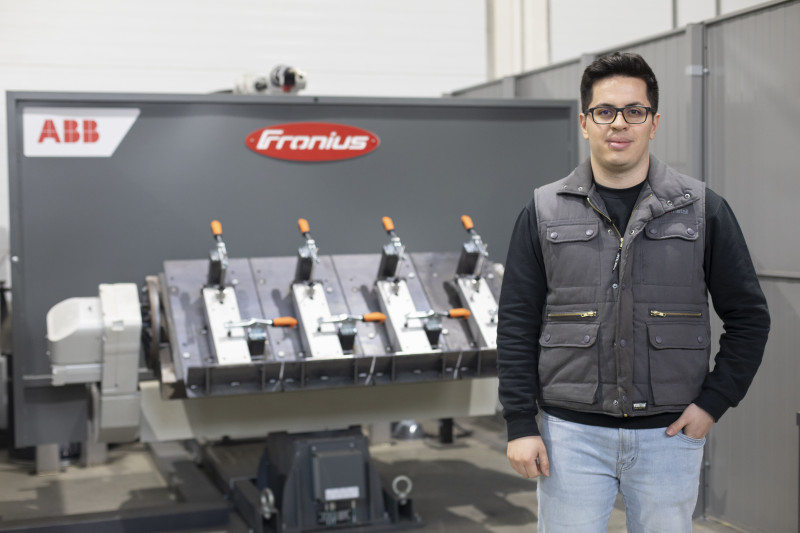
Standardization with iWave Pro in robotic welding cells
Viñolas Metall has been placing its faith in Fronius since 2016, when the first TPS/i welding system for intelligent MIG/MAG welding was introduced. Recently the company has been facing a new challenge: the welding robot must weld various components using both the TIG and MIG/MAG process – with rapid process changes and programmed configurations. Welding quality and system stability must be kept constant throughout.
“The reliability of the equipment and service quality of technology partners are key factors for us,” emphasizes David Viñolas. “The Fronius support team fully supported us during the test phase of the new iWave Pro. We have now purchased four more devices.”
On Viñolas Metall’s journey towards Industry 5.0, the iWave Pro stands out for its compatibility with WeldCube, the advanced Fronius welding data management and documentation software. Further advantages include the CycleTig and PMC (Pulse Multi Control) functions, which significantly contribute to the reduction in uneconomical rework. The optional DynamicWire Welding Package, enabling dynamic wirefeed during manual TIG welding, is another plus. The devices are robust and feature a long service life with low maintenance, significantly improving the ecological footprint. Their large digital color display is easy to use even with welding gloves.
(Source: Fronius Press Release)
Schlagworte
CMTIndustry 5.0MAGMIGRoboticsRobotsTIGWelding