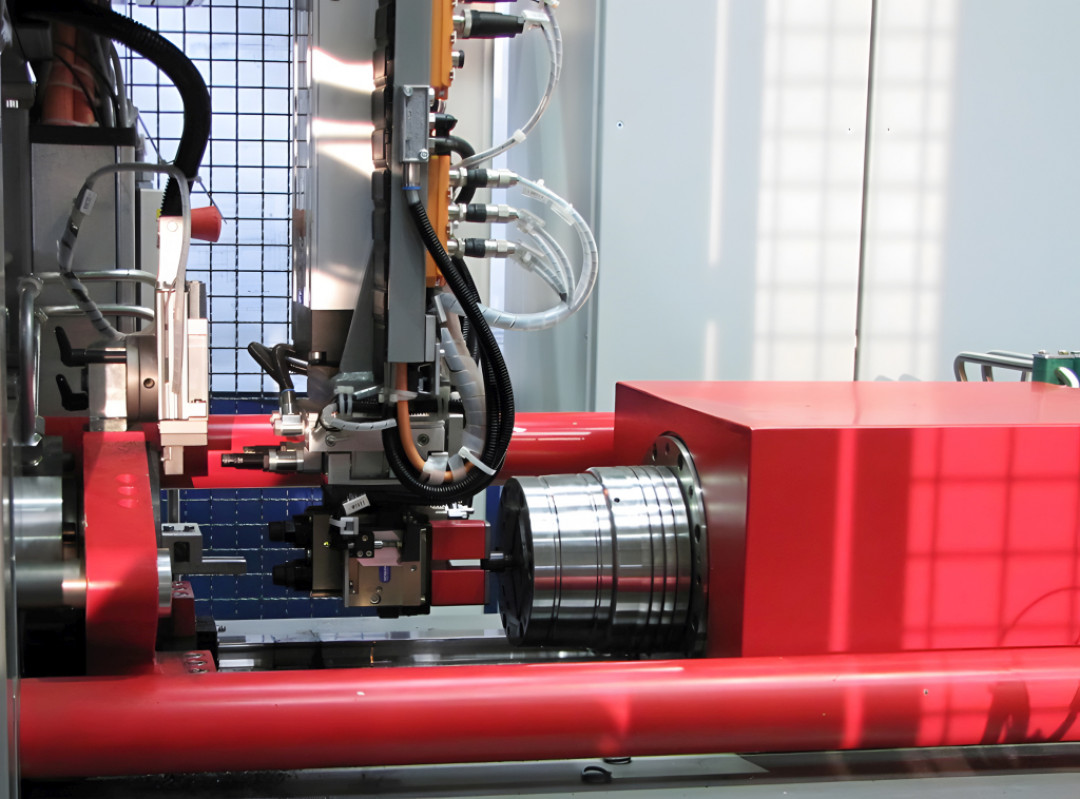
Reibschweißen: Von der Standalone-Maschine bis zur automatisierten Fertigungszelle
Reibschweißen gehört zu den sichersten Fügeverfahren der modernen Fertigungstechnik. Es verbindet Komponenten schnell, sicher und wirtschaftlich und ist für die Produktion in vielen Industriezweigen von essentieller Bedeutung. Reibschweißmaschinen der Klaus Raiser GmbH & Co. KG versprechen nicht nur eine hohe Schweißnahtqualität, kurze Taktzeiten und hohe Prozesssicherheit, sondern arbeiten auch hochpräzise und energieeffizient – dank des wohl durchdachten Reibschweißmaschinen-Konzeptes.
Seit fast 50 Jahren hat sich die Klaus Raiser GmbH & Co. KG auf das Reibschweißen spezialisiert und ist zu einem führenden Unternehmen auf diesem Gebiet geworden. Die Faszination für diese Technologie begann im Jahr 1973, als der Firmengründer, Klaus Raiser, sie auf einer Messe entdeckte. Was ihn sofort begeisterte, war die Möglichkeit, zwei Werkstücke aus unterschiedlichen Materialien nur durch Reibung und Druck miteinander zu verbinden – ohne zusätzliche Energie. Diese einzigartige Methode hat Raiser dazu inspiriert, nicht nur im Lohnreibschweißen tätig zu sein, sondern auch eigene Reibschweißmaschinen zu entwickeln und zu bauen.
Ausgeklügeltes Reibschweißmaschinen-Konzept
Die jahrzehntelange Erfahrung mit dem Verfahren beim Lohnreibschweißen hat Raiser in die Entwicklung und den Bau von Reibschweißmaschinen einfließen lassen. Die Projektleitung dafür findet sich am Standort in Magdeburg. Dort entwickeln und konstruieren erfahrene Ingenieure die Maschinen und auch die Spannmittel für Werkstücke. Gebaut werden sie schließlich am Firmensitz in Eberdingen. Durch diese Erweiterung der Kompetenzen ist Raiser als Fullservice-Anbieter für das Reibschweißen – von der Prozessentwicklung, über Lohnfertigung im Klein- und Großserienbereich bis hin zur fertigen Maschine.
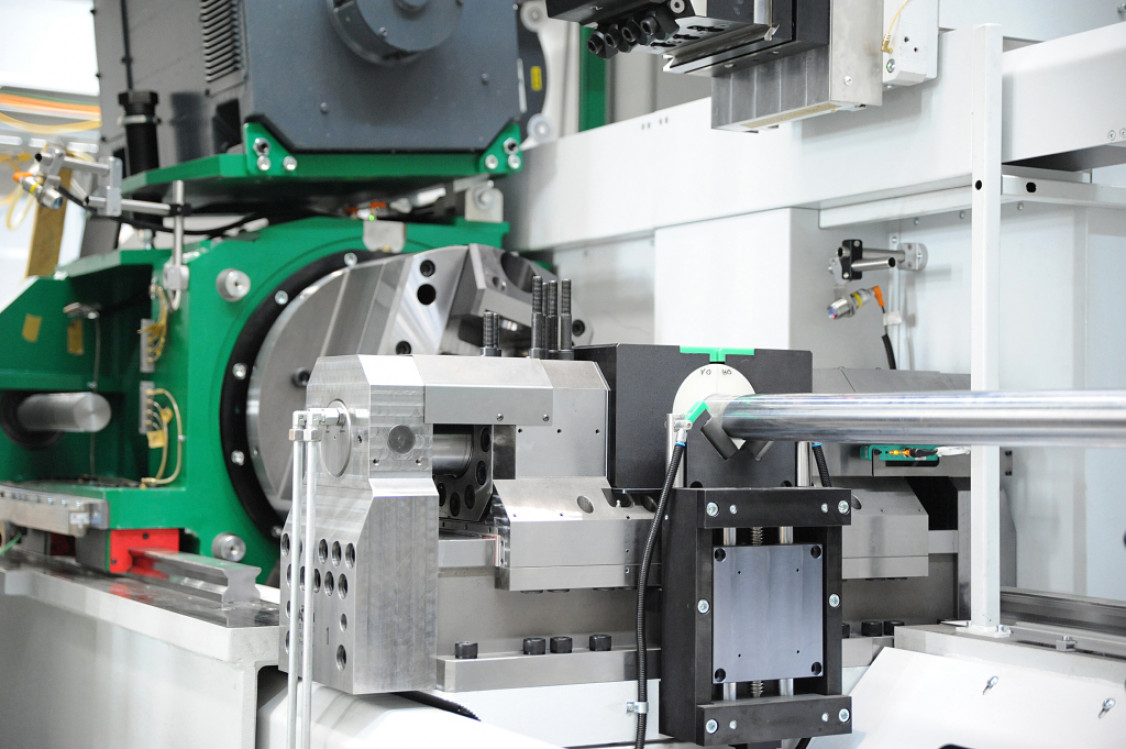
„Das Besondere an unseren Reibschweißmaschinen ist die Bewegung in axialer Richtung: Im Gegensatz zu den meisten anderen Reibschweißmaschinen am Markt bewegt sich der Rotor – also das in Rotation gebrachte Werkstück – und der Stator steht fest“, erklärt Christian Mann, Vertriebsingenieur bei Raiser. „Dafür setzen wir zudem einen servoelektrischen Antrieb für den Vorschub ein und keinen hydraulischen wie andere Marktbegleiter. Die Kugelgewindespindel mit einem Vorschubmotor samt Riemen oder mit Direktantrieb fährt die Arbeitsspindel mit dem Bauteil auf das stehende, im Stator eingespannte Bauteil zu. Dabei schützen Teleskopbleche die Führungen der Kugelrollspindel vor dem Zunder beim Reibschweißen bzw. vor den Spänen beim Abdrehen der Wulst. Dieses Maschinenkonzept bringt zahlrieche Vorteile mit sich.“
Energie sparen mit Raiser Reibschweißmaschinen
Der servoelektrische Antrieb sorgt für eine bessere Energieeffizienz. Warum? Bei einem hydraulischen Vorschub muss die Hydraulik permanent laufen, um immer Öl im Kreislauf zuhalten – selbst wenn die Maschine nicht arbeitet. Das ist bei Raiser anders. Eine frequenzgeregelte Hydraulik wird bei Raiser Reibschweißmaschinen nur für die Spannung der Bauteile in der Maschine verwendet, wenn eine höhere Spannkraft gefordert ist. Bei kleineren Maschinen verzichtet Raiser gänzlich auf die Hydraulik und setzt je nach geforderter Spannkraft mechanische Aktuatoren (z.B. Federn), servoelektrisch betätigte oder pneumatisch betätigte Spannmittel. Die Hydraulikaggregate fallen deshalb entsprechend klein aus und laufen auch nur bei Bedarf. Ansonsten ist die Hydraulik ausgeschaltet. Das verringert den Energieverbrauch der Reibschweißmaschine auf ein Minimum und damit auch den ökologischen Fußabdruck. Ein weiteres Plus: Die Lärmemission wird ebenfalls auf ein Minimum beschränkt.
Der Spindelkörper ist darüber hinaus mit einer Kraftsensorik gekoppelt. Diese misst die Kraft, die auf die Arbeitsspindel mit dem Werkstück wirkt – direkt und ohne Umwege. Bei einem Vorschub über einen hydraulisch bewegten Kolben wird die Kraft über Druck je Fläche berechnet. Der Anwender kann somit nicht ohne genaue Flächenmaße die am Bauteil wirkende Kraft ermitteln bzw. präzise einstellen. „Bei unseren erübrigt sich dieser Aufwand. Egal wie groß die Maschine ist (500 kN oder 1.000 kN), der Anwender gibt immer die Kraft ein, welche am Bauteil wirken soll. Die Folge: Jedes Bauteil kann auf einer Raiser Reibschweißmaschinen geschweißt werden – und das völlig unkompliziert“, so Christian Mann.
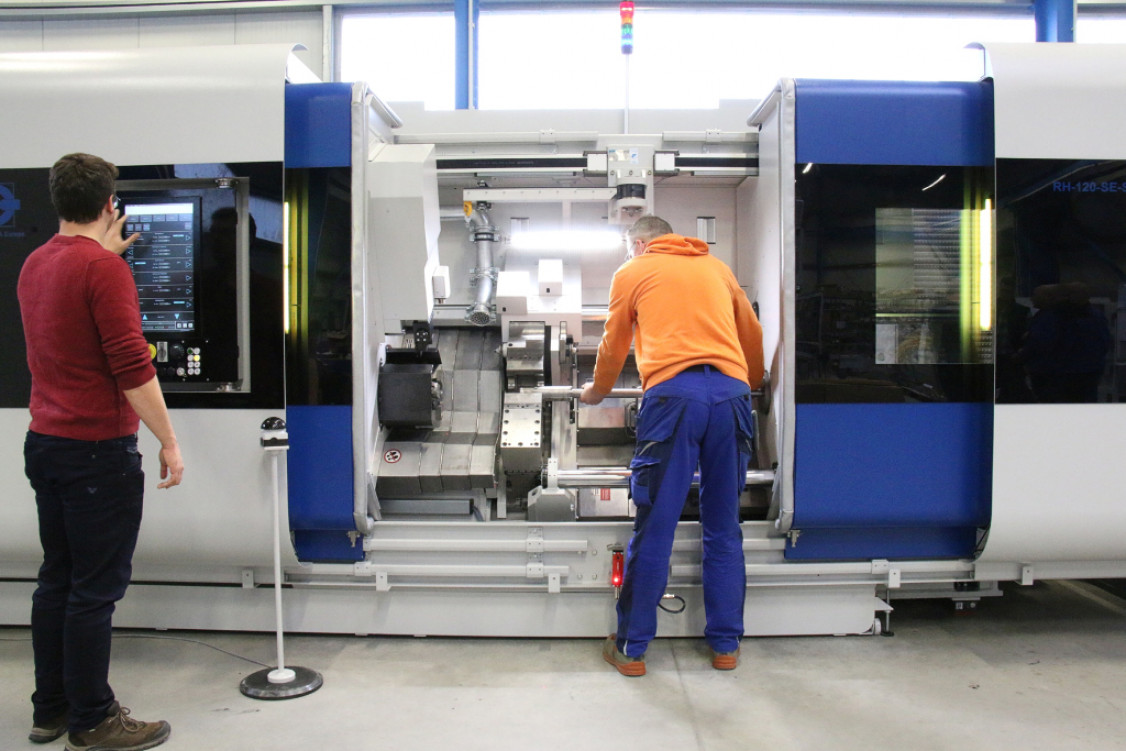
Reibschweißmaschinen für höchste Präzision
Die Rotationsbewegung, um die Reibungswärme im Schweißprozess zu erzeugen, wird über einen Direktantrieb mittels frequenzgeregeltem Einbaumotor auf der Spindelwelle realisiert. Dank des servoelektrischen Einbaumotors kann die Spindel umgehend und drehwinkelgenau zum Stehen gebracht werden. Daraus ergibt sich eine Winkelpositioniergenauigkeit von theoretisch minimal 0,1° genau – je nach abzubremsender Masse.
Christian Mann: „Dank des generatorischen Bremsens der Spindel kann zudem Energie zurückgewonnen und ins Netz gespeist werden. Dadurch lassen sich die Spannungsspitzen, die beim Reibschweißen entstehen, abflachen und der Gesamtenergieverbrauch sinkt.“
Dank des kompakten Designs benötigen die Reibschweißmaschinen nicht nur wenig Stellfläche, sondern sind sie auch in punkto Rundlaufgenauigkeit im Vorteil: Denn da nur kleine, leichte Teile auf geringem Raum bewegt werden müssen, entstehen keine Unwuchten. Ein Glasmaßstab (Absolutwertgeber) sorgt zudem für die genaue Längenposition beim Reibschweißen. Das ist ein Gesamtpaket für höchste Präzision!
Individuelle Konfiguration ist Standard
Raiser realisiert verschiedene Maschinentypen mit einer Stauchkraft zwischen 1 und 2.000 kN. Dabei können die Experten vertikale und horizontale Reibschweißmaschinen mit Flachbett oder Schrägbett, mit oder ohne Einhausung umsetzen. Wer ein Bauteil wie zum Beispiel eine Kardanwelle von zwei Seiten gleichzeitig bearbeiten und die Taktzeit halbieren will, kann statt einer Einkopfvariante mit einer Spindel eine Doppelkopfmaschine erhalten. Dabei bietet Raiser die Reibschweißmaschinen in verschiedenen Ausbaustufen an: Das Maschinenkonzept lässt dem Anwender die Wahl zwischen einer Standalone-Maschine mit manueller Beladung, einer geschlossenen Fertigungszelle mit unterschiedlichen Automationslösungen oder eine ganz und gar die den vollautomatisierten Workflow integrierten Anlage.
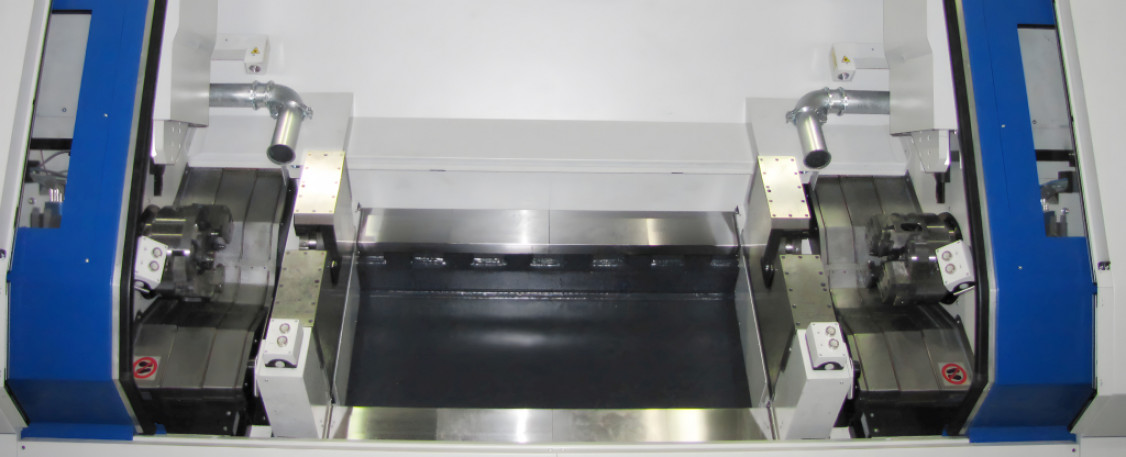
Raiser Reibschweißmaschinen werden standardmäßig mit einem großen schwenkbaren 21,5“ Multitouchpanel ausgestattet. Mit der Integration von Service- und Bedienungsanleitung, aller Handfunktionen, USB- und Ethernet Schnittstellen sowie mit einer kundenspezifischen Auswahl an Hardtastern wird für hohe Flexibilität und Gestaltungsfreiraum bei der Entwicklung innovativer Bedienkonzepte gesorgt. Zur Grundausstattung gehört ebenfalls eine Siemenssteuerung, die ein gewohntes Programmier- und Bedienungslayout für den Anwender mitbringt. Jede Maschine ist mit Safety Integrated ausgestattet und wird mit CE-Konformität ausgeliefert.
„Darüber hinaus lassen sich zahlreiche zusätzliche Optionen in unsere Reibschweißmaschinen integrieren: Das reicht von Dreh- und Fräsprozessen oder Abschermodulen zum Entfernen der Wulst sowie Revolvern mit bis zu vier angetriebenen Werkzeugen über eine Werkzeugbruchkontrolle, Werkstückausheber und Manipulatorhandling zum Beladen der Maschine bis hin zu Traceability, Luftanlagenkontrolle, Bauteilabfragen und redundante Messsysteme & Signalverarbeitung sowie vielem mehr. Wir sind da ganz offen für die Wünsche und Anforderungen unserer Kunden“, ergänzt Christian Mann.
Angepasste Werkstückspannung inklusive
Auf der Statorseite müssen oft sehr komplexe und auch mitunter empfindliche Komponenten eingespannt werden. Bei Raiser erhalten Anwender deswegen auf Wunsch auch die Entwicklung und Konstruktion einer bauteilabgestimmten Werkstückspannung. Damit werden die Bauteile während des Prozesses auf keinen Fall beschädigt und die Produktivität gesichert. Je nach Bedarf können unterschiedlichste komplexe und weniger komplexe Vorrichtungen auf der Statorseite montiert werden.
Weitere Informationen:
Klaus Raiser GmbH & Co. KG
Zeppelinring 6
71735 Eberdingen (Hochdorf)
Germany
Tel.: +49 7042 88105-0
Fax: +49 7042 88105-50
E-Mail: info@raiser.de
(Quelle: Presseinformation der Klaus Raiser GmbH & Co. KG)
Schlagworte
AutomationEnergieeffizienzFertigungFertigungszellenFügetechnikPräzisionReibschweißenReibschweißmaschinenSchweißnähte