ARTIKEL DES MONATS
Trendthema

Autor: J. Delskamp, Bergmann & Steffen GmbH, Spenge (www.bergmann-steffen.de)
Remote-Laserstrahlschweißen: Gebläse-Crossjet für Scanner-Anwendungen
Remote-Laserstrahlschweißen erfreut sich aufgrund der hohen Dynamik und der mannigfaltigen Vorteile steigender Beliebtheit. Betriebswirtschaftlich stehen dem aber hohe Betriebskosten entgegen. Das neuartige Gebläse-Crossjet „Tornadoblade“ hilft nun die Betriebskosten solcher Remote-Laserstrahlschweißanlagen zu senken und wirkt sich positiv auf die Prozessstabilität aus. Dies ist von entscheidender Bedeutung für die erfolgreiche und wirtschaftliche Umsetzung einer Schweißaufgabe.
Laser finden in vielen Anwendungsbereichen Verwendung, beispielsweise zum Schweißen, Schneiden oder zum Oberflächenbearbeiten und stellen mittlerweile ein industrielles „Standardwerkzeug“ dar. Die heute verwendeten Laserstrahlleistungen für das Schweißen von Metallen betragen mehrere Kilowatt. Besonders im Automobilbereich gewinnen zunehmend hochproduktive sogenannte Remote-Laserstrahlschweißoptiken an Bedeutung. Diese werden im Regelfall an einen Industrieroboter adaptiert, über ein Lichtleitkabel mit der Laserstrahlquelle verbunden und positionieren den Laserstrahl über schnelle Umlenkspiegel. Durch zudem große Brennweiten bzw. einem großen Arbeitsabstand von bis zu 1 m besteht die Herausforderung auch in der langen „freien“ Strecke für den Laserstrahl bis
hin zum Werkstück. Innerhalb dieses Arbeitsraums wird der Laserstrahl mit der – insbesondere durch den Schweißprozess selbst verunreinigten – Atmosphäre interagieren. Streuungs- und Abschirmungseffekte führen hier zu Leistungsverlust am Werkstück, reduzieren die Qualität des Laserstrahls und führen zu Prozessinstabilitäten.
Diese äußern sich in Form von Auswurf flüssiger Metallschmelze. Diese Schweißspritzer können leicht bis zur Schweißoptik fliegen und sich dort auf den optisch vergüteten Flächen absetzen und anhaften. Deshalb werden Remote-Laserstrahlschweißoptiken durch systembedingt große Schutzgläser (Durchmesser ungefähr 130 mm, Stückkosten rund 125 €) vor dem Schweißprozess selbst geschützt. Um die Standzeit dieser Verschleißartikel zu verlängern, wird konventionell ein quer zum Laserstrahl angeordneter, starker Luftstrom eingesetzt. Dazu werden jedoch große Mengen an Druckluft benötigt (etwa 2.500 Nl/min = 150 m³/h; Systemdruck typischerweise 8 bar), deren Bereitstellung und Erzeugung zu hohen Investitions- und Betriebskosten führen. Zudem kommen unplanmäßige Maschinenausfallzeiten für den Austausch des Schutzglases hinzu.
Entwicklung
Der Entwicklungsansatz im Jahr 2013 bestand also darin, eine Lösung zur Senkung der Betriebskosten zu finden. Je nach Fall können nach dem zuvor beschriebenen konventionellen Druckluftkonzept leicht 10.000 € pro Jahr und Schweißkopf überschritten werden. Doch die alleinige Substitution von durch Kompressoren erzeugter Druckluft durch deutlich günstigere Gebläseluft stellte keine praxistaugliche Errungenschaft dar. Der Schlüssel zum Durchbruch lag in der gesamten Neugestaltung der Düseneinheit.
Im weiteren Entwicklungsverlauf, sowie ersten Tests im hauseigenen Applikationslabor zeigten sich weitere positive Effekte wie eine Verbesserung der Schweißqualität sowie das Potenzial zu Taktzeiteinsparung und eine erhöhte Programmierfreiheit für Roboterbahnen. Testphasen bei Anwendern aus dem Automotive-Bereich waren derart erfolgreich, sodass ein Erstausrüster bereits alle seine Remote- Laserstrahlschweißoptiken nachgerüstet hat. Die neuartige Prozessdüse „Tornadoblade“ ist nun also in der Lage, die Schweißoptiken zu schützen, die Betriebskosten der Laserschweißanlage nachhaltig zu senken und die Stabilität des Laserschweißprozesses selbst zu erhöhen.
Verfahrensprinzip
Ein Niederdruckgebläse erzeugt kostengünstig einen hochvolumigen Luftstrom, der in eine unter der Optik angeordnete Ringkammer eingeleitet und in Rotation versetzt wird (Bild 1a). Dieser strömt dann durch eine nach schräg unten gerichtete Ringdüse aus (Bild 1b). Es ergibt sich durch diesen Aufbau der Düseneinheit ein kräftiger, in sich rotierender Luftstrom, der von der Schweißoptik ausgehend in Richtung Werkstück gerichtet ist (Bild 1c).
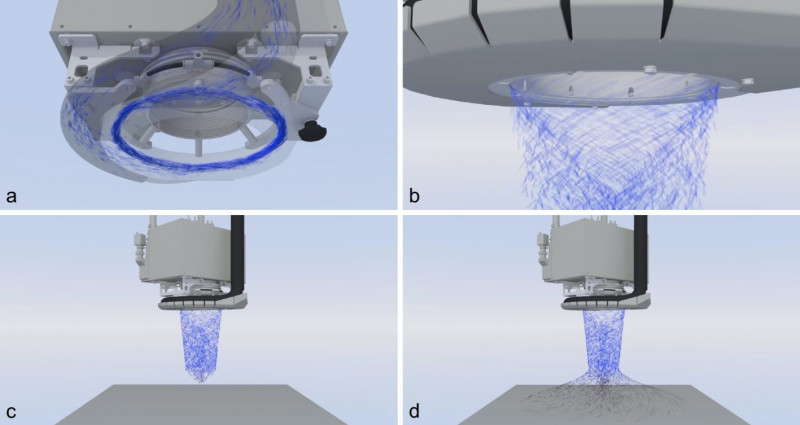
Neben der Schutzwirkung für die Remote-Laserstrahlschweißoptik werden dadurch zusätzlich Schweißrauch und Partikel aus dem freien Weg des Laserstrahls entfernt. Der Laserstrahl breitet sich also in einer relativ sauberen Atmosphäre aus, und Streuungseffekte werden reduziert.
Da der Luftwirbel bis auf das Werkstück reicht, übernimmt der Gebläse-Crossjet zusätzlich die direkte Belüftung der Schweißstelle. Metalldämpfe und Schweißrauche werden so direkt am Entstehungsort „nach außen“ weggeblasen, energiereichere Schweißspritzer werden zumindest so weit nach außen abgelenkt, dass Sie die Optik, das heißt das Schutzglas, nicht mehr erreichen können (Bild 1d). Es bildet sich ein glockenähnlicher Druckkegel aus, wobei eine tangentiale Komponente für eine Rotation des Luftwirbels in sich sorgt.
Gerätetechnik
Die Düseneinheit des Tornadoblade wird direkt an die Laserstrahlschweißoptik montiert. Dazu werden die Befestigungsbohrungen der Gerätehersteller verwendet. Bild 2 zeigt den prinzipiellen Aufbau im Querschnitt. Die direkt an die Laserstrahlschweißoptik anschließende Spülluftbaugruppe beaufschlagt das Schutzglas über eine radiale Zuführung mit geringen Mengen sauberer und trockener Druckluft, um durch das sich gleichmäßig ausbildende Überdruckpolster einer Kontamination der Schutzglasoberfläche mit Staub und Rauch entgegenzuwirken. Die Ringdüsenbaugruppe ist mit einem definierten Abstand unter der Spülluftbaugruppe angeordnet. Dieser Systemaufbau führt dazu, dass durch umlaufende Eintrittsöffnungen Umgebungsluft nachströmt und der aus der Ringdüse austretende Gebläseluftstrom durch den sogenannten Coanda-Effekt nochmals verstärkt wird.
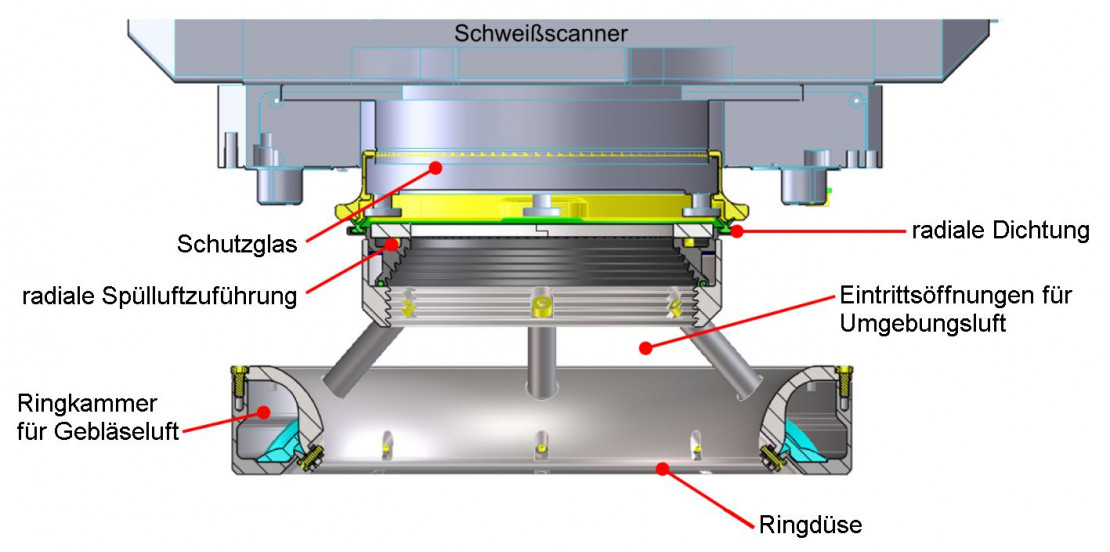
Praxis und Schweißergebnisse
Bild 3 veranschaulicht die Wirkungsweisen der Schutzmechanismen für Remote-Optiken – im oberen Teil schematisch, darunter ist eine entsprechende Aufnahme des realen Schweißprozesses zu sehen. Der linke Teil zeigt das konventionelle Prinzip des mit Druckluft betriebenen Crossjets: Die im Schweißprozess entstehenden Spritzer und Rauche steigen ungehindert im Arbeitsraum der Laserstrahlschweißoptik auf, bis sie kurz unterhalb der Optik durch einen dazu rechtwinklig angeordneten Luftstrom abgelenkt werden. Unregelmäßiges Absorptionsverhalten in diesem Bereich verursacht Prozessinstabilitäten, die durch geringere Schweißgeschwindigkeit oder höhere Laserstrahlleistung ausgeglichen werden müssen.
Im rechten Bildteil ist das Tornadoblade-Prinzip dargestellt: Der primär von oben wirkende Luftstrom hält den Arbeitsraum frei, sodass der Schweißprozess unter stets stabilen Umgebungsbedingungen stattfinden kann. Entstehende Partikel werden direkt am Entstehungsort erfasst, niedergehalten und nach außen gedrückt. Besonders auffällig ist zunächst einmal eine deutliche Reduzierung des Prozessleuchtens (blau). Das Bild zeigt auch, wie Schweißrauch und Schweißspritzer bereits am Entstehungsort abgelenkt werden (grün). Unter dem Gebläse-Crossjet ergibt sich Raum, der frei von Schweißspritzern und Schweißrauch ist (gelb).
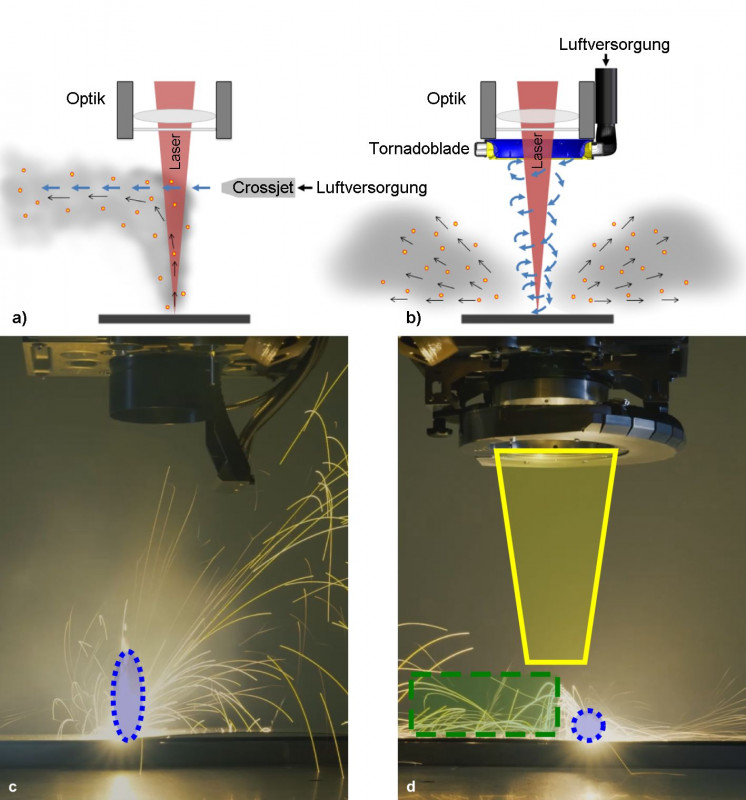
Bild 4 zeigt Schliffproben zu Einschweißversuchen in 4 mm dickem, unbeschichtetem St1203-Blech mit gleichenProzessparametern (Fokusdurchmesser dFok = 640 μm, Laserstrahlleistung P = 5 kW, Schweißgeschwindigkeit v = 100 mm/s), jedoch unterschiedlichen Belüftungsvarianten. Die drei Schliffe unterschieden sich erheblich hinsichtlich Schweißnahtbreite und Einschweißtiefe. Wird keinerlei Belüftungstechnik eingesetzt, so ergibt sich eine flachere, breitere Schweißnaht (Bild 4a). Die tiefste und schmalste Laserstrahlschweißnaht wird unter Verwendung einer optimal positionierten Druckluftdü- se und Schweißrichtung gegen den Luftstrom erzielt (Bild 4b). Der Gebläse-Crossjet liegt hinsichtlich Schweißnahtbreite und Einschweißtiefe jeweils zwischen den beiden genannten (Bild 4c).
Auffällig ist zudem der leichte Nahteinfall bei Einsatz der Druckluftdüse. Zu vermuten ist hier, dass flüssiger Werkstoff in Form von Schweißspritzern ausgeblasen wurde. Hier versteckt sich ein weiterer Vorteil bei Verwendung des Tornadoblade: Es lassen sich unabhängig von der Schweißrichtung bzw. der Bewegungsrichtung des führenden Roboters gleichmäßige Schweißergebnisse erzielen. So kann beispielsweise eine Umorientierungsbewegung vermieden und somit Taktzeit eingespart werden.

Schlussbemerkungen
Es ist zwingend erforderlich die Schutzgläser von Laserstrahlschweißoptiken vor Schweißspritzern und Schweißrauch zu schützen, da bereits geringe Anhaftungen und Ablagerungen unweigerlich zu Leistungsverlust, Prozessinstabilitäten und nachfolgend zur Beschädigung und letztendlich Zerstörung des Schutzglases führen. Nach geltendem Stand der Technik werden Schweißoptiken und die beinhalteten Schutzgläser durch Druckluft-Crossjets vor Schweißspritzern geschützt. Der hier vorgestellte Gebläse-Crossjet kann die Betriebskosten einer Laserstrahlschweißanlage aufgrund des deutlich geringeren Energieverbrauches und der besseren Schutzwirkung – abhängig von der Anwendung – erheblich reduzieren. Als Nebeneffekt werden Schweißqualität und Reproduzierbarkeit der Schweißverbindungen verbessert, da der Einfluss von Störfaktoren deutlich reduziert wird. Das Tornadoblade ist verfügbar für verschiedene Typen der Hersteller Trumpf, Scanlab und Highyag.
Schlagworte
LaserstrahlschweißenRemote-LaserstrahlschweißenSchweißqualität