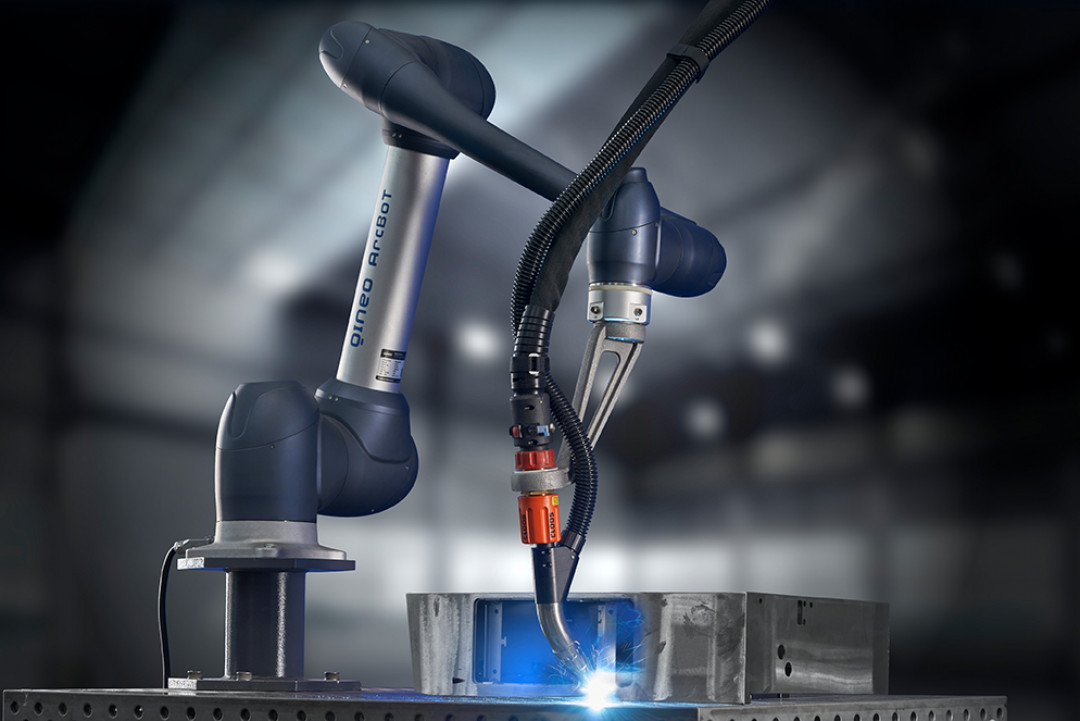
Easy entry into automation
Partial automation solutions such as cobots are now also established in the field of welding and offer an easy start into automation. At the exhibition, CLOOS will present the QINEO ArcBoT, where employee, cobot and welding power source optimally complement each other – a solution approach for companies to compensate for the increasing shortage of skilled workers. With the QINEO ArcBoT Welding System, users can weld even small batch sizes economically and with consistently high quality. In addition to the relief of the employees – especially with monotonous, repetitive tasks – companies benefit from excellent welding results due to the reproducible quality. The new extended functions such as seam tracking increase the efficiency of cobot welding even further. The QINEO ArcBoT at SCHWEISSTEC is equipped with a torch-integrated welding fume extraction system that provides safe and effective extraction of welding fumes directly at the source.
CLOOS will also be presenting the new QIROX robot QRC-350-EO at the SCHWEISSTEC trade fair. Thanks to its eccentric axis 7, which is specially designed for overhead applications, the robot can be optimally integrated into complex system concepts. The space requirement of the robot system is reduced to a minimum. The QIROX system includes the robot technology, positioners, safety technology, software, sensors and the interface to the process technology. The CLOOS portfolio comprises simple, compact standard systems as well as complex, chained systems with automated workpiece identification and loading and unloading processes. The modular design provides users with scalable solutions that are optimally adapted to different applications and individual production requirements - whether small, delicate workpieces or large, complex components.
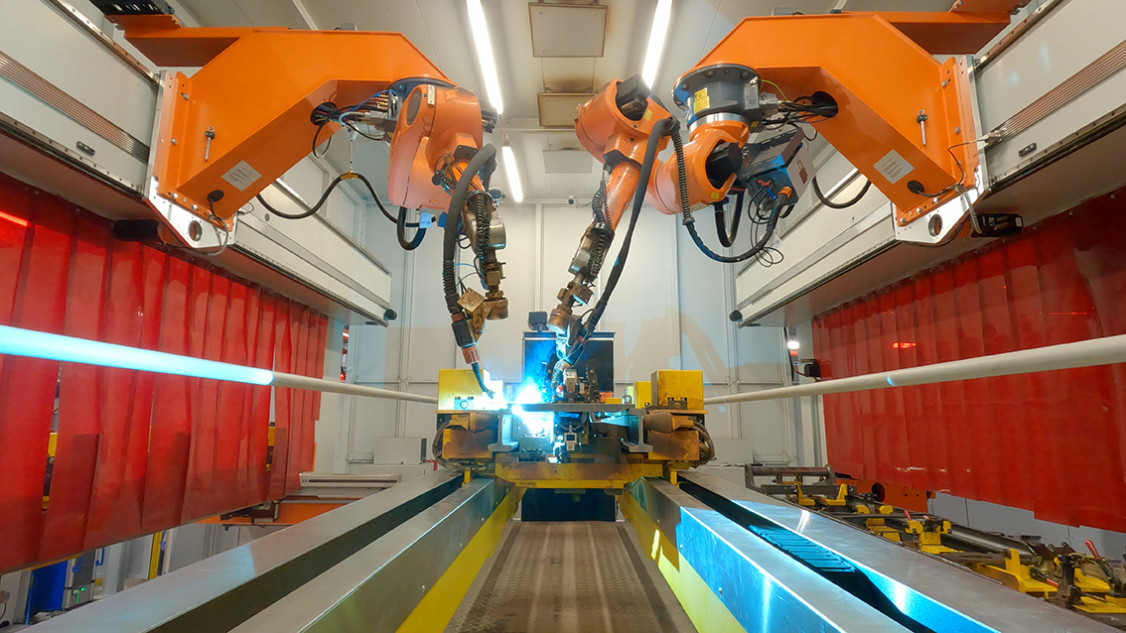
Manual Welding from Entry to Premium
During live-demonstrations of manual welding trade visitors can experience the constantly rising model range of the QINEO welding power sources from entry to premium. With the new Mix Weld process users can solve demanding welding tasks even with heat-sensitive materials. Vertical-up welds and horizontal-vertical positions can also be welded linearly with this process which significantly saves time in the process sequence.
CLOOS Weldin Technology: Robot and Welding Technology from a Single Source
Since 1919, Carl Cloos Schweisstechnik GmbH has been one of the leading companies in welding technology. More than 900 employees all over the world realise production solutions in welding and robot technology for industries such as construction machinery, railway vehicles, energy, automotive and agricultural industry. The modern CLOOS welding power sources of the QINEO series are available for a multitude of welding processes. With the QIROX robots, positioners and special purpose machines CLOOS develops and manufactures automated welding systems meeting the specific requirements of the customers. The special strength of CLOOS is the widely spread competence. Because – from the welding technology, robot mechanics and controller to positioners, software and sensors – CLOOS supplies everything from a single source.
The QINEO StarT allows an easy start into the world of modern MIG/MAG welding technology. Due to the optimum price-performance ratio, users can weld any workpiece at economic conditions. The high-tech QINEO NexT MIG/MAG welding power source convinces by excellent arc characteristics for highest welding quality. The modular design allows many utilisation possibilities – from the basic welding machine for manual welding to the multiprocess welding machine for automated robot welding.
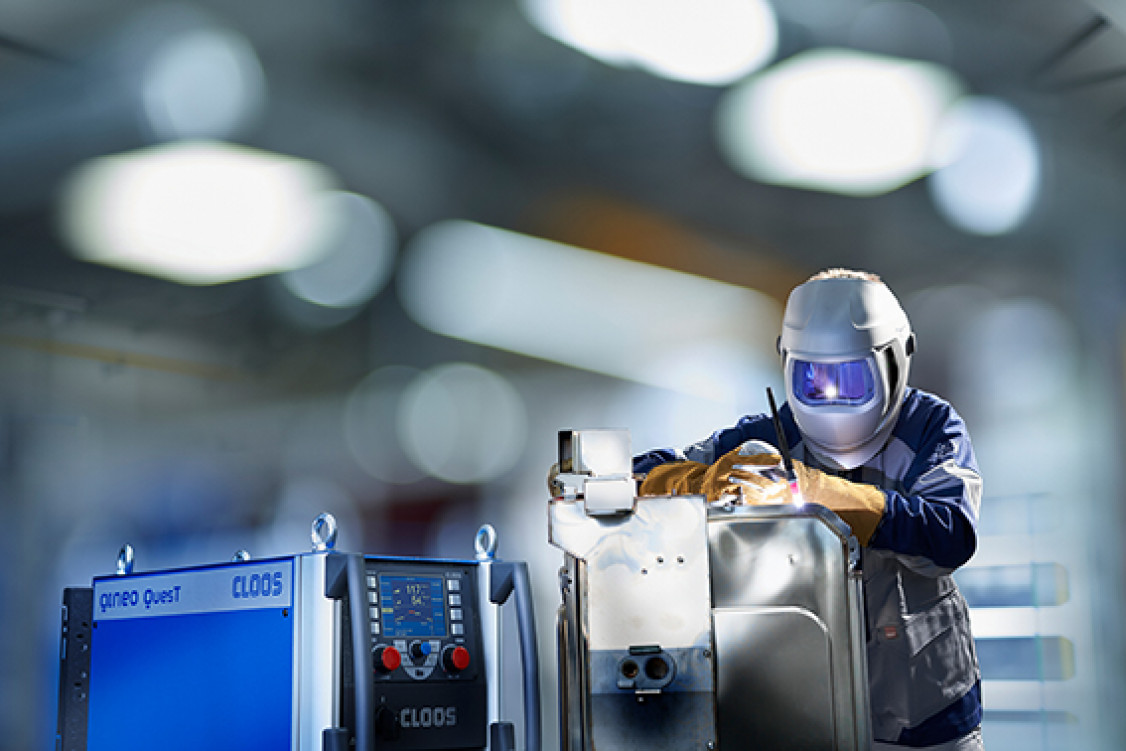
Digitisation Solutions for Future Production
The CLOOS software solutions increase the performance of welding power sources and robot systems in addition. With the C-Gate IoT platform, users can access information from their welding production in real time. The central data acquisition and processing allows users to monitor and control their production processes down to the smallest detail. C-Gate consists of several modules which users can activate depending on their individual digitalisation strategy – consistently from the manual welding power source to the fully automated production line.
(Source: Cloos Press Release)
Schlagworte
AutomationCobotsRoboticsSchweisstecWelding