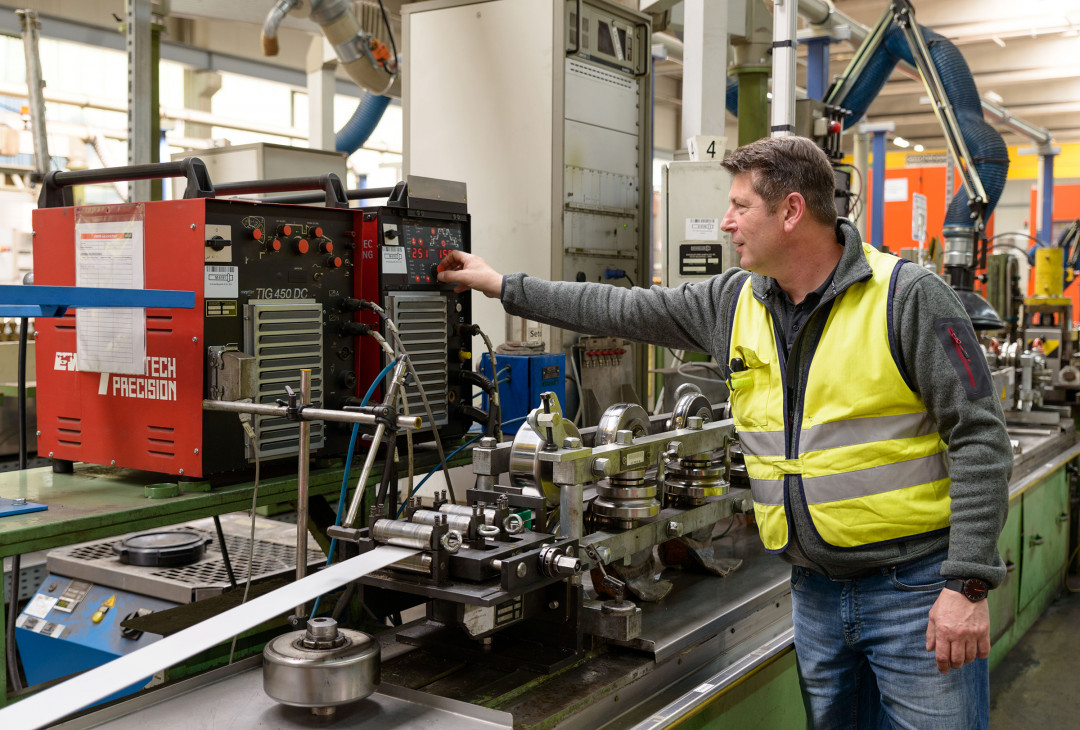
EWM-Kunde der ersten Stunde
Möglich ist das auch dank der langjährigen Zusammenarbeit mit EWM. Bereits seit 1995 ist Schoeller Kunde des deutschen Schweißtechnikherstellers. Die Besonderheit dabei: EWM produziert überhaupt erst seit 1993 eigene Schweißgeräte. Davor war das Unternehmen als Komponentenhersteller auf dem internationalen schweißtechnischen Markt vertreten. Das Schoeller Werk ist somit Kunde der ersten Stunde, seit EWM den Wandel zum Gerätehersteller vollzogen hat. In den fast 25 Jahren hat das Unternehmen EWM stets die Treue gehalten. „Früher haben wir klassische Schweißgleichrichtertechnologie verwendet. Das waren robuste, schwere Geräte mit viel Kupfer. Wir hatten wenige Einstellungsmöglichkeiten: Entweder lieferte das Gerät Strom oder nicht“, erinnert sich Stefan Fink, Abteilungsleiter Instandhaltung/Technik bei Schoeller. Er arbeitet seit 34 Jahren im Unternehmen und kennt die Geräte von der Pike auf. Durch den Kontakt zum Schweißinstitut der Rheinisch-Westfälischen Technischen Hochschule (RWTH) Aachen führte das Unternehmen schließlich die Inverter-Technologie ein. Der Schweißgerätehersteller, mit dem Schoeller zuvor zusammenarbeitete, hatte diese Technologie jedoch noch gar nicht im Portfolio. Somit folgte der Wechsel zu EWM.
Gemeinsam Entwicklungen vorantreiben
Die Zusammenarbeit zwischen Schoeller und EWM war von Beginn an durch ein gutes Vertrauensverhältnis, schnelle Reaktionszeiten und zuverlässigen Service geprägt. Ändern sich die Anforderungen an die Geräte, reagiert EWM sofort. „EWM investiert außerdem viel in die eigene Forschung und Entwicklung, wodurch sich für uns die Möglichkeit ergibt, gemeinsam neue Entwicklungen voranzutreiben“, erläutert Stefan Fink. Schoeller hat eine Testanlage, wo das Unternehmen Versuche mit neuen EWM-Technologien durchführt. Ein Ergebnis: Früher hat Schoeller nur WIG-geschweißt, heute nutzt das Unternehmen auch WIG-Plasma-Technologie. Auch bei der Entwicklung neuer Schoeller-Produkte trug die Kooperation bereits Früchte. Als sich das Unternehmen 2008 dazu entschloss, künftig auch Railrohre herzustellen, gelang dieser Schritt schlussendlich auch durch die Zusammenarbeit mit EWM. Heute ist Schoeller der führende Produzent von Railrohren europaweit.
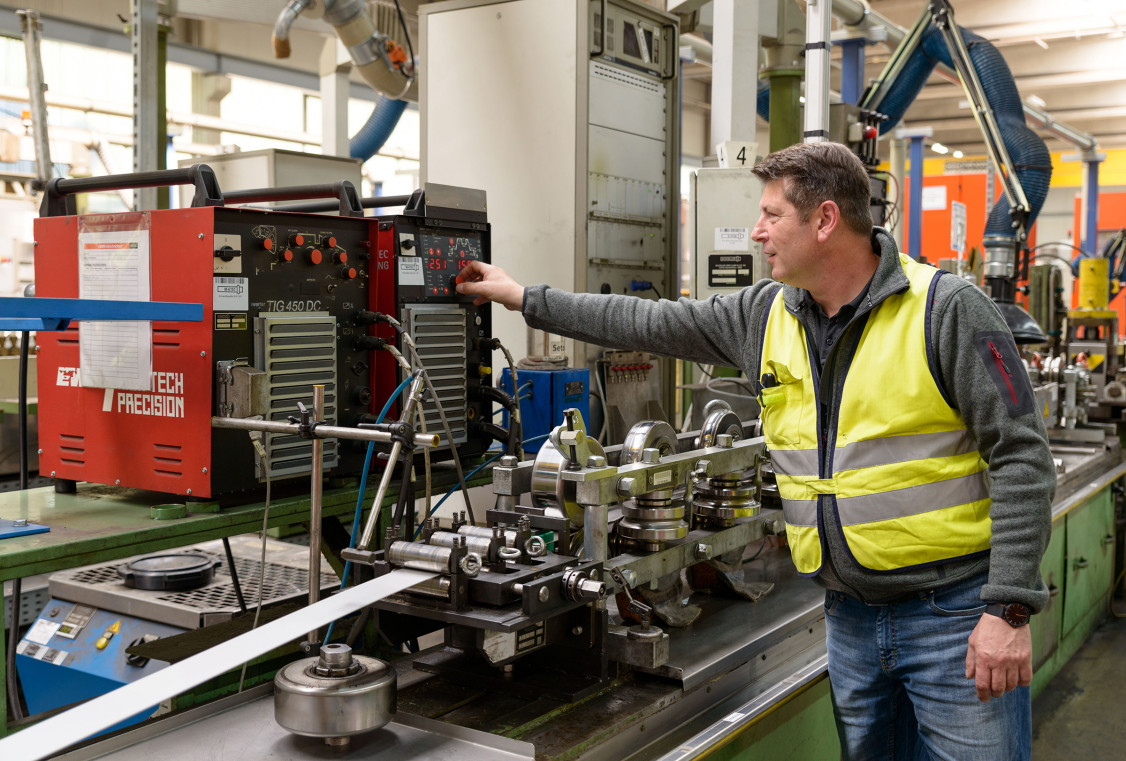
Schweißgeräte individuell auf Schoeller zugeschnitten
Eine besondere Anforderung an die Schweißgeräte stellt nicht nur die Unterstützung bei der Entwicklung neuer Produkte bei Schoeller, sondern auch allgemein die hohe Belastung dar. Denn die Maschinen in Hellenthal laufen von sonntag- bis samstagabends nonstop. Hinzu kommt, dass die Wandstärken der Rohre zunehmend dicker werden, wodurch sich die Strombelastung der einzelnen Geräte erhöht. Gemeinsam mit EWM hat Schoeller daher die Schweißgeräte individuell auf die eigenen Bedürfnisse zugeschnitten. Vor allem die Steuerung, die die präzise Bedienung der Geräte ermöglicht, enthält einige Schoeller-Spezifikationen. „Wenn wir bei EWM ein Schweißgerät bestellen, dann ist das nie ein Gerät von der Stange“, erklärt Stefan Fink.
Schoeller prüft und repariert Geräte selbst
Damit die Mitarbeiter von Schoeller Geräteprüfungen selbständig durchführen können, haben einige von ihnen an Schulungen von EWM am Stammsitz in Mündersbach (Rheinland-Pfalz) teilgenommen. Früher schickte Schoeller die Geräte ein oder ein Außendienstmitarbeiter von EWM kam ins Werk. Bei mittlerweile 300 Geräten im Einsatz ist es für das Unternehmen effizienter, dafür eigenes Personal einzusetzen. Sicherheitsprüfungen der Schweißgeräte führt Schoeller in einem jährlichen Turnus daher selbst durch. Das Unternehmen nutzt das tragbare Kalibrier- und Validiergerät von EWM, das eigens dafür angeschafft wurde. „Wir arbeiten bei unseren Prüfzirkeln mit einem Maintenance-Tool, das anzeigt, welche Geräte aktuell geprüft werden müssen. Der Standardtest dauert maximal 15 Minuten und ist somit schnell durchgeführt, sofern das Gerät keine Auffälligkeiten aufweist“, erklärt Stefan Fink. Sollte es in seltenen Fällen zu Auffälligkeiten kommen, verlässt sich Schoeller weiterhin auf den Service von EWM. Muss ein Gerät zur Wartung, kann Schoeller auf eines seiner Austauschgeräte zurückgreifen.
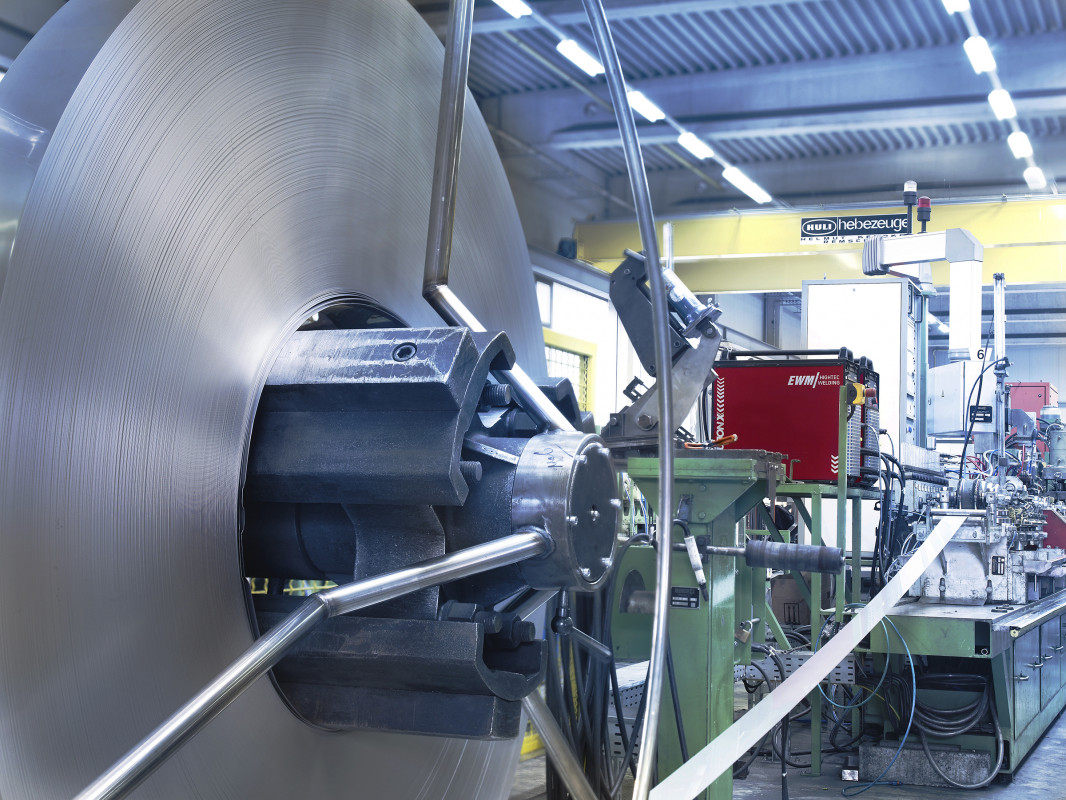
EWM-Geräte meistern besondere Anforderungen
Neben der schnellen Austauschbarkeit der Geräte innerhalb der eigenen Maschinenanlagen stellt Schoeller seit vielen Jahren besondere Anforderungen an die Schweißgeräte von EWM: Sie müssen schnittstellenkompatibel sein, einer hohen Belastung im Dauereinsatz standhalten, eine hohe Stromstabilität aufweisen und flexibel sowohl an den neuen als auch an den älteren Anlagen einsetzbar sein. Da die Geräte von EWM kompakt sind, kann Schoeller sie nah am jeweiligen Einsatzort innerhalb der Produktionsstraße integrieren. Stefan Fink zieht daher abschließend ein positives Fazit: „Die Zusammenarbeit mit EWM läuft bestens. Die kompetenten Mitarbeiter suchen auch kurzfristig nach Lösungen mit uns. Durch das langjährige Vertrauensverhältnis habe ich Ansprechpartner bei EWM, die ich bereits fast so lange kenne, als wären wir gemeinsam zur Schule gegangen.“
(Quelle: Anwenderbericht der EWM AG)
Schlagworte
EdelstahlLaserschweißenSchweißenWIG SchweißenWIG-Plasma-Schweißen