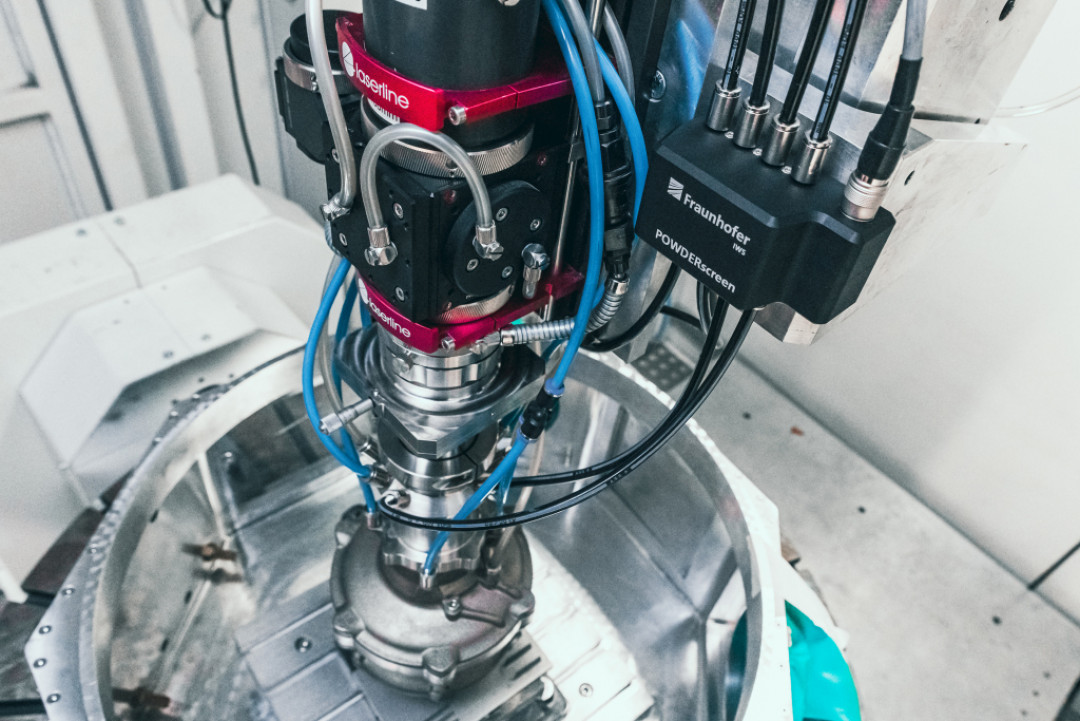
POWDERscreen überwacht Pulverströme in die Laserschmelze
Additive Fertigungsverfahren spielen im Automobilbau, der Raumfahrt und weiteren Branchen eine wachsende Rolle: Wenn komplex geformte Bauteile beziehungsweise Unikate herzustellen sind, setzen immer mehr Unternehmen auf den industriellen 3D-Druck. Allerdings können die Einlaufkurven gerade bei Kleinserien noch recht lang und die Ausschussquoten anfangs groß sein. Das Fraunhofer-Institut für Werkstoff- und Strahltechnik IWS Dresden entwickelt daher moderne Mess- und Regeltechnik, mit der sich additive Verfahren viel effektiver als bisher einsetzen lassen, zum Beispiel für hochautomatisierte Fertigungsstrecken. Dazu gehört der POWDERscreen – ein einzigartiges Pulvermessgerät für das Laserauftragschweißen. Das Fraunhofer IWS demonstriert dieses innovative System im Mai 2022 während der „3. Fachtagung Werkstoffe und Additive Fertigung“ im Deutschen Hygiene-Museum Dresden.
Konzipiert ist POWDERscreen für das Laserauftragschweißen. Bei diesem additiven Fertigungs-, Beschichtungs- und Reparaturverfahren fördern Spezialdüsen konzentrierte Ströme aus Metallpulver genau in den Fokus eines Laserstrahls. Der schmilzt das Pulver auf der Werkstückoberfläche auf, um aus dieser Schmelze komplexe 3D-Strukturen zu erzeugen. Mit dem Pulverstrommessgerät lässt sich künftig genau ausmessen, welche Metalle in welcher Menge in den Laserfokus strömen. Dieser Ansatz kann die Kosten beim pulverbasierten Laserauftragsschweißen senken, die Qualität der erzeugten Bauteile verbessern und den ganzen Produktionsprozess exakt wiederholbar gestalten – gerade dies ist in der Hightech-Industrie eine besonders wichtige Anforderung.
Wichtiger Schritt zu einem geregelten Fertigungsprozess
„Bisher bleibt das pulverbasierte Laserauftragschweißen noch immer hinter seinen Möglichkeiten zurück“, schätzt Rico Hemschik ein. Der Ingenieur am Fraunhofer IWS hat POWDERscreen entwickelt. „Mit dem Pulverstrommessgerät gehen wir einen großen Schritt hin zu einem effizienteren, geregelten und automatisierten additiven Fertigungsprozess.“
Um dies zu ermöglichen, kombiniert das System moderne Sensorik mit spezieller Software, einem Bildschirm sowie Schnittstellen für die Datenübergabe.
Photosensoren zählen hier die Partikel im Pulverstrom, die Software berechnet daraus die Fördermengen. Der Bildschirm zeigt dem Maschinenführer die aufbereiteten Daten an.
Ein besonderer Vorteil ist die universelle Einsatzfähigkeit: Der POWDERscreen lässt sich an jeden Prozesskopf für das Pulver-Laserauftragschweißen montieren. Ein Anwendungsbeispiel, in dem der POWDERscreen seine Stärken besonders gut ausspielt, ist die Düse COAXquattro. Dieser Prozesskopf wurde am Fraunhofer IWS entwickelt, um bis zu acht verschiedene Pulver oder Drähte in getrennten Kanälen in den Laserfokus zu fördern und dort In-situ-Legierungen zu erzeugen. Da die COAXquattro pro Kanal bis zu 30 Gramm je Sekunde unterstützt, lassen sich hier erhebliche Pulverraten erzielen. Wegen der großen Fördermengen eignet sich die Kombination aus COAXquattro und POWDERscreen besonders für Hochleistungsprozesse, in denen große und komplexe Bauteile mit hoher Qualität, Reproduzierbarkeit und Geschwindigkeit erzeugt, beschichtet oder repariert werden müssen.
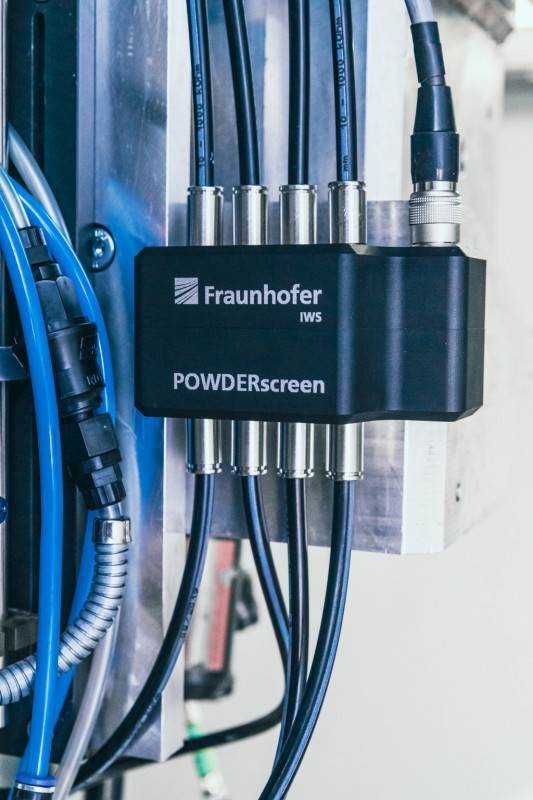
Automatische Genese von „Digitalen Zwillingen“ möglich
Solche kombinierten Prozessüberwachungssysteme sollen künftig auch selbstständig Digitale Zwillinge von additiv erzeugten Bauteile generieren. Denn die Informationen darüber, an welcher Stelle der Laser welches Pulver in welcher Menge aufgeschmolzen, legiert und geformt hat, lassen sich prinzipiell auch automatisiert zu einem virtuellen Computermodell zusammenführen. Mit herkömmlichen Methoden wäre es schwer bis unmöglich, solche lokalen Legierungsveränderungen innerhalb eines Bauteils exakt zu modellieren.
Große Einsatzpotenziale für POWDERscreen sehen die Forschenden am Fraunhofer IWS unter anderem in der Luft- und Raumfahrt. Dort lässt sich das System beispielsweise einsetzen, um kompliziert geformte Turbinenschaufeln mit additiven Verfahren in gleichbleibend hoher Qualität zu reproduzieren und zu reparieren. Ähnliches gilt für Prägewerkzeuge im Automobilbau oder die Prototypenfertigung quer durch nahezu alle Industriebranchen.
Wenn Maschinenführer in Zukunft pulverbasierte Laserauftragsschweißanlagen nicht mehr „freihändig“ und mit vielen Versuchen einrichten müssen, sondern auf der Basis exakt erfasster und wiederholbarer Prozessparameter, dann liegen die Vorteile auf der Hand: Die Einlaufkurve verkürzt sich, die Ausschussquote zu Beginn einer Kleinserie sinkt. Zudem werden die Prozesse dadurch effizienter und in hoher Qualität reproduzierbar. Nicht zuletzt lassen sie sich künftig automatisiert dokumentieren – was wiederum wichtig für spätere Garantiefälle sein kann.
(Quelle: Presseinformation des Fraunhofer-Instituts für Werkstoff- und Strahltechnik IWS)
Schlagworte
3D-DruckAdditive FertigungLaserauftragschweißenLasertechnologienMesstechnik