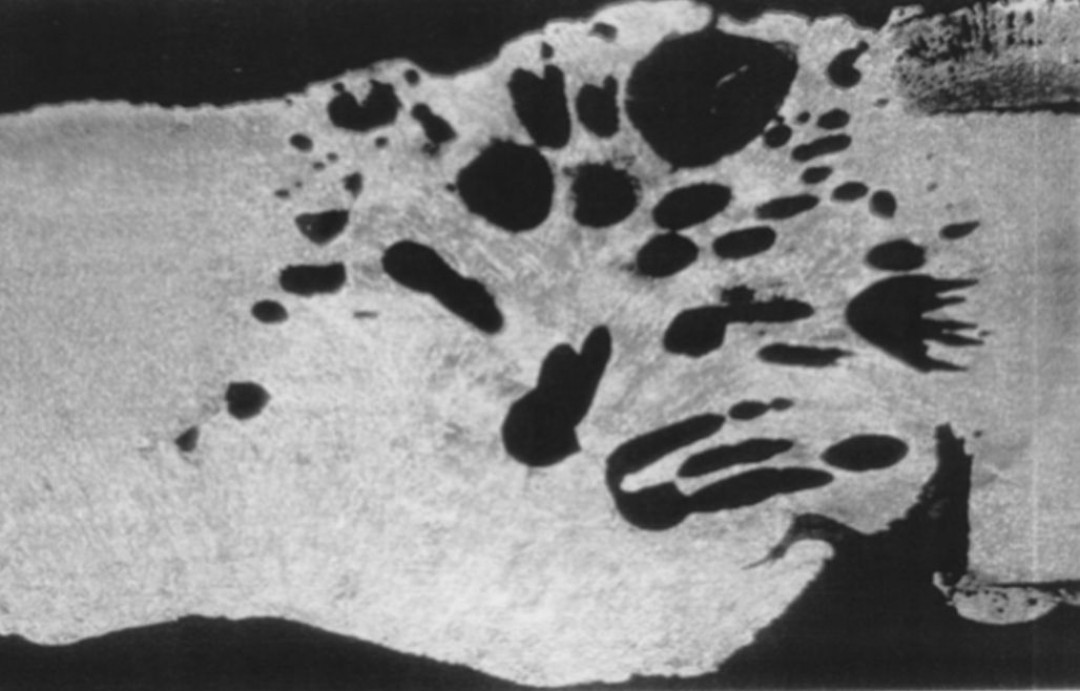
Untersuchungsschritte bei Schadensfallanalysen
Beweissicherung und Bestandsaufnahme
Einem Schweißbetrieb, der dem Vorwurf ausgesetzt ist, Bauteile aus seiner Fertigung haben durch Risse oder Brüche den Ausfall der Konstruktion verursacht, wird empfohlen, möglichst viele Informationen über das geschädigte Bauteil oder die geschädigte Anlage und den Schadensablauf zu sammeln. Mit Kenntnis der Ursache des Bauteil- bzw. des Schweißnahtversagens kann gegebenenfalls nachgewiesen werden, dass von seiner Seite nichts falsch gemacht wurde. Bei einer Bestandsaufnahme sind möglichst alle Informationen über die Anlage bzw. das Bauteil, die Vorgeschichte und den Schadenshergang zu sammeln. Eine Checkliste [4] kann dabei helfen, alles Wesentliche zu erfassen. Auch wenn ein Schweißbetrieb nur mit der Reparatur beauftragt wurde und nicht direkt in die Schadensfallanalyse einbezogen war, sollte der Auftraggeber vor Auftragsannahme befragt werden, welche Kenntnisse er zur Schadensursache besitzt, weil das für den Aufwand und den Ablauf einer fachgerechten schweißtechnischen Reparatur für das ausführende Unternehmen von entscheidender Bedeutung ist.
Informationen in Checkliste sammeln
- Welche Funktion und Beanspruchungen der Anlage bzw. des Bauteils gibt es?
- In welche Ausführungsklassen EXC 1 bis EXC 4 nach DIN EN 1090 sind die beanstandeten Konstruktionsteile eingestuft worden, und hatten das herstellende Unternehmen und die Montagefirma die dafür erforderlichen Eignungsnachweise?
- Besteht seitens des Herstellers noch die Gewährleistungspflicht?
- Wann wurden die Schäden festgestellt?
- Wie viele Baugruppen oder Bauteile sind betroffen?
- An welchen Bauteilen oder Baugruppen befinden sich die Brüche und/oder Risse?
- Gibt es Werksabnahmeprotokolle für die auf der Baustelle angelieferten Bauteile?
- Wie kann der Schaden beschrieben werden?
- Sind die beanstandeten Schweißnähte Werkstattnähte, oder wurden sie auf der Baustelle mit den beanstandeten Mängeln geschweißt?
- Welche Unterlagen gibt es für die schweißtechnische Vorbereitung und Ausführung der beanstandeten Nähte?
- Gibt es Nachweise zu Rissfreiheit und Nacharbeiten und anderes mehr? Wenn ja, von wem wurden diese erstellt und kontrolliert? Welche normalen und anormalen Betriebsbedingungen gab es beim Schadenseintritt?
- Ist die Anlage noch betriebsfähig, oder ist es ein Totalausfall?
- Können die geschädigten Bauteile wieder schweißtechnisch instandgesetzt werden, oder sind sie durch neue Bauteile zu ersetzen?
- Wurden die schadhaften Bauteile sichergestellt?
- Von wem wurden die Schäden festgestellt?
- Wurde ein Mängelprotokoll erstellt, und an wen wurde es gemeldet?
- Kann der Schadensablauf zeitlich eingegrenzt werden?
- Wann erfolgte die letzte Inspektion der schadhaften Bauteile bzw. Anlagenkomponenten?
- Waren die Bediener eingewiesen und mit der Anlage vertraut?
- Ist der Schaden erstmalig oder zum wiederholten Mal aufgetreten?
- Gab es bereits schweißtechnische Reparaturen – wann und welche?
- Von wem wurden die schweißtechnischen Reparaturen durchgeführt?
- Die Schadensstelle bzw. das Bauteil sollten für makroskopische Schadensbeurteilungen der Riss- und Bruchverläufe zum Beispiel durch Fotos und/oder Probenentnahmen gesichert werden.
- Welchen Bewertungsgruppen nach DIN EN ISO 5817 sind die festgestellten Unregelmäßigkeiten zuzuordnen?
- Wer führte bei der Ausführung der Schweißarbeiten die Schweißaufsicht?
- Welche konstruktiven und fertigungstechnischen Besonderheiten des Bauteils bzw. der Anlage gibt es?
- Der sonstige Zustand des Bauteils im Schadensbereich sollte erfasst werden.
- Welche sonstigen Beobachtungen, zum Beispiel Beläge, Anlauffarben, außergewöhnliche Lageveränderungen, gibt es?
- Gab es bereits Probenentnahmen für Werkstoffanalysen, metallografische und/oder rasterelektronenmikroskopische Untersuchungen zum Beispiel der Bruchflächen und anderes mehr in neutralen zertifizierten Prüfinstituten?
- Ist das noch nicht erfolgt, sind erforderliche Probenentnahmen festzulegen und zu kennzeichnen.
- Die technischen Spezifikationen bzw. weiteren Dokumentationen zum Fertigungsablauf in den vertraglichen Unterlagen sind zu überprüfen in Hinblick auf
- konstruktive Details zur schweißtechnischen Ausführung in den Zeichnungen,
- Berechnung und Bewertung von statischen und veränderlichen Beanspruchungen,
- zu beachtende Regelwerke für Gestaltung und Ausführung,
- einzusetzende Werkstoffe,
- schweißtechnische Ausführung (WPS),
- vorgesehene Bewertungsgruppen nach DIN EN ISO 5817,
- mechanische und zerstörungsfreie Prüfungen der Schweißverbindungen,
- Wärmevor- und Wärmenachbehandlungen sowie
- weitere durchgeführte protokollierte Abnahmeprüfungen, zum Beispiel Druckprüfungen.
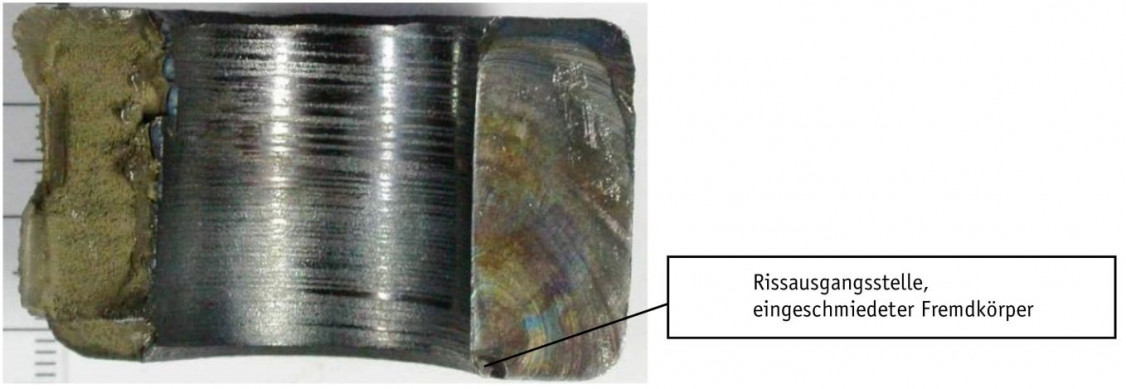
Auswertung vorliegender Daten und Dokumentationen
Die bis dahin gesammelten Daten können nun bewertet und die Schadensbilder zum Beispiel mit bekannten Versagensformen verglichen werden. Dazu gehört die Auswertung charakteristischer Schadensmerkmale, zum Beispiel Bruchart, Bruchlage und Bruchaussehen. Die Beurteilung der Bruch- und/oder Rissstelle an Schweißverbindungen stellt einen äußerst wichtigen Untersuchungsschritt bei der Aufdeckung möglicher Schadensursachen dar. Bei der Beurteilung der Bruchfläche nach der Bruchart lässt sich ablesen, ob es zum Beispiel ein
- zäher Gewaltbruch,
- Sprödbruch,
- Dauer- oder Ermüdungsbruch
ist.
Metallografische Untersuchungen decken auf, ob es sich um inter- oder transkristalline Bruchverläufe handelt. Hinsichtlich von Bruch- und Risslage ist bei Schweißverbindungen zu unterscheiden, ob das Versagen eingetreten ist durch Längs- oder Querrisse, offene oder verdeckte Risse. Weiterhin ist zu untersuchen, ob die Rissenden eindeutig erkennbar sind und ob die Risse von den Schweißnähten, der Wärmeeinflusszone, vom Grundwerkstoff, von Unregelmäßigkeiten der Schweißnaht, zum Beispiel Einbrandkerben, von der Schweißnahtwurzel, zum Beispiel bei Kehlnähten, oder von innen liegenden Bindefehlern oder Einschlüssen ausgehen.
Hinsichtlich der Rissarten ist bei Schweißverbindungen zu unterscheiden zwischen:
- Heißrissen durch Wiederaufschmelzungsrisse, Erstarrungsrisse,
- Kaltrissen infolge von Härtespitzen, Kerb- und Wurzelrissen, Spannungsrissen, wasserstoffinduzierten Rissen,
- Lamellenrissen infolge von zeilenförmigen Einschlüssen im Grundwerkstoff, zum Beispiel Mangansulfidzeilen, Oxide und
- Relaxationsrissen infolge von Relaxationsversprödung durch Ausscheidungsvorgänge an den Korngrenzen, zum Beispiel beim Spannungsarmglühen.
Das Bruchaussehen lässt Schlüsse zu, ob es fertigungsbedingte und/oder beanspruchungsbedingte Risse sind. Die Bruchflächen können zum Beispiel folgende Merkmale haben:
- grobkristallin und zerklüftet,
- feinkörnig,
- korrodiert oder metallisch blank,
- Anlauffarben,
- Rastlinien eines Ermüdungsbruchs,
- unterschiedliche Größen der Ermüdungsund Gewaltbruchflächen (Bilder 6 bis 8).
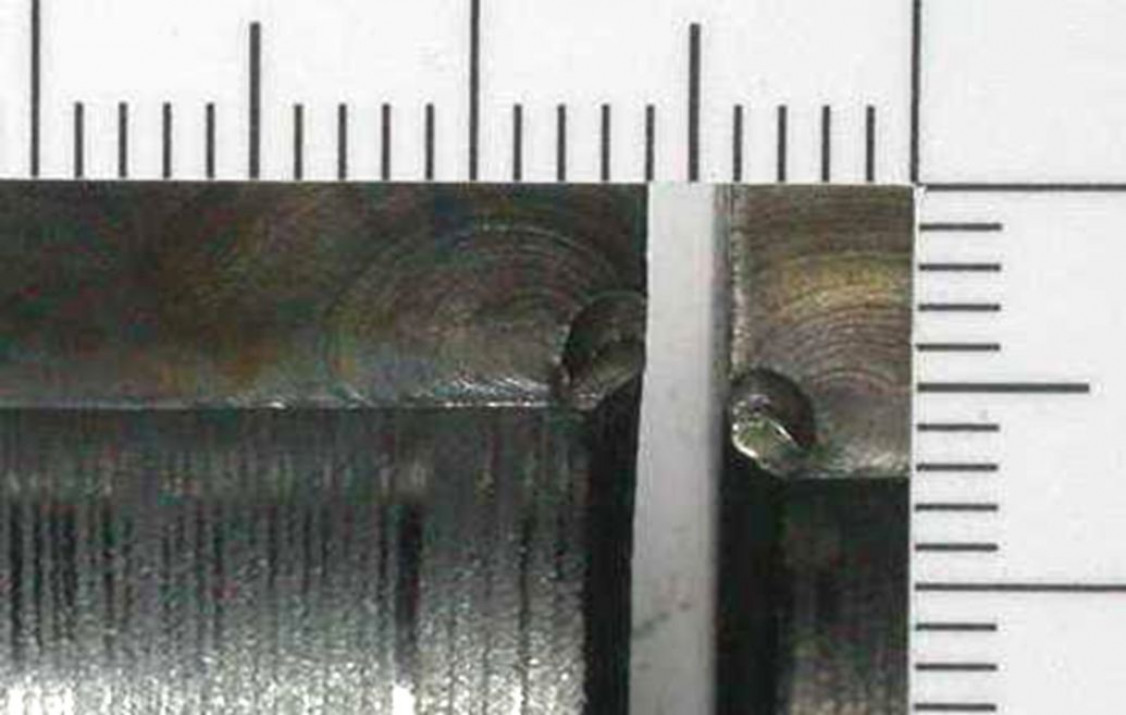
Das Größenverhältnis der Ermüdungs- und Gewaltbruchflächen zueinander (Bild 8) schließt hier sowohl eine Überbeanspruchung als auch eine Unterdimensionierung aus. Eventuell wurde etwas angeschweißt, was ursprünglich gar nicht vorgesehen war.
Am Kehlnahtübergang gab es vermutlich einen Anriss, der sich bei veränderlichen Beanspruchungen nach und nach immer weiter ausbreitete.
Rastlinien sind ein Indiz dafür, dass die veränderlichen, meistens schwingenden Belastungen sich hin und wieder abschwächten und der Ermüdungsbruch zeitweilig ruhte, rastete. Erst mit dem weiteren Auftreten der veränderlichen Belastungen vergrößerte sich die Ermüdungsbruchfläche so weit, bis der Restquerschnitt so klein geworden war, dass er durch Gewaltbruch endgültig versagte.
Um weitere Belege für die Ursachen des eingetretenen Schadens zu sammeln, kann es erforderlich werden,
- die Wand- und Nahtdicken nochmals auszumessen,
- vorhandene Nahtunregelmäßigkeiten bzw. Schweißnahtfehler den in den Konstruktionszeichnungen geforderten Bewertungsgruppen nach DIN EN ISO 5817 gegenüberzustellen,
- Werkstoffdaten, zum Beispiel chemische Zusammensetzung, mechanischtechnologische Gütewerte, Gefügebeschaffenheit (Makro- und Mikroschliffe), Härtemessungen, zu überprüfen.
Weitere dahingehend zu beachtende Punkte:
- Bei vermuteten Überbeanspruchungen oder Unterdimensionierungen sind die Bauteil- und Schweißnahtbeanspruchungen rechnerisch zu kontrollieren.
- Sind bei der Berechnung die konstruktiven und schweißtechnisch bedingten Kerbfälle entsprechend den geltenden Regelwerken beachtet und bei der Dimensionierung berücksichtigt worden?
- Welche Berechnungsmodelle wurden verwendet (Nenn-, Struktur- oder Kerbspannungsmodelle)?
- Vergleichsschweißverbindungen an entnommenen Werkstoffproben können etwas über den Alterungszustand der Werkstoffe aussagen.
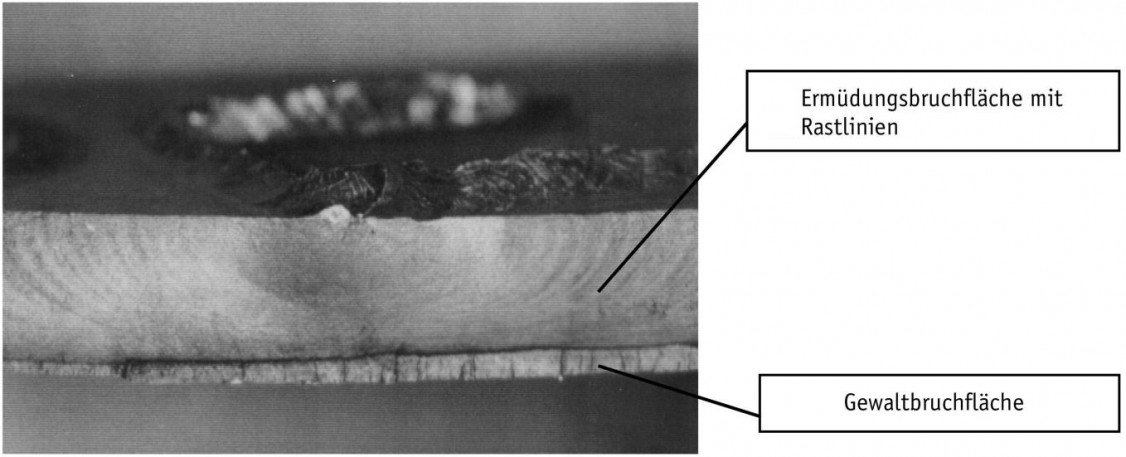
Schadensursache ermitteln
Mit den bis dahin gesammelten Erkenntnissen lässt sich meistens eine Versagenshypothese für die Schadensursache aufstellen bzw. ein Plan für notwendig erscheinende weitere Untersuchungen erarbeiten. Es geht darum, die Versagenshypothese beweiskräftig zu untermauern und die Schadensursache eindeutig zu benennen (Bild 9). Das ist die Grundlage für die Entscheidung, ob der Hersteller oder der Betreiber den Schaden verursacht hat bzw. wessen Versicherung die Kosten für Produktionsausfall, Reparatur oder Ersatzleistungen trägt. Bestehen darüber noch immer Zweifel oder unterschiedliche Auffassungen, sind weitere Untersuchungen – wie beschrieben – in die Wege zu leiten.
Es ist im ureigenen Interesse sowohl des herstellenden Schweißbetriebs als auch des Betreibers herauszufinden, welches die Hauptursachen für den eingetretenen Schaden waren und wer damit der Hauptverursacher ist, der dann auch die Kosten zu tragen hat. In der Praxis führt häufig die Überlagerung von mehreren sich gegenseitig beeinflussenden Ursachen zum Bauteilversagen. Die Kenntnis der Hauptursachen von Schäden ermöglicht die fachgerechte schweißtechnische Instandsetzung, weil zum Beispiel Schäden infolge von Ermüdungsbelastungen oder Korrosion aufwendigere Reparaturlösungen erfordern als Schäden infolge von statischen Überbelastungen. Auch notwendige konstruktive Änderungen von Querschnitten und Schweißnahtdetails zur Verbesserung der Beanspruchbarkeit bei schwingender Belastung bzw. des Werkstoffeinsatzes für eventuelle Ersatzkonstruktionen können damit begründet werden. Nach erfolgter schweißtechnischer Instandsetzung kann durch zusätzliches Einebnen der Schweißnahtoberflächen bei Stumpfnähten bzw. Nachbehandeln der Nahtübergänge durch Kugelstrahlen, Nadelhämmern oder Ultraschallhämmern zum Beispiel die Lebensdauer der reparierten Bauteile bei schwingender Beanspruchung verlängert werden.
Die Kenntnis der Schadensursache im Zusammenhang mit der Reparaturlösung ist die Voraussetzung zur Abschätzung der verbleibenden Restlebensdauer der instandgesetzten Bauteile. Weil man aus Fehlern lernen kann, sind die teuer erkauften Kenntnisse des Bauteilversagens sowohl für den Hersteller als auch für den Betreiber wertvoll und hilfreich. Nicht zuletzt ist die ermittelte Schadensursache Grundlage für versicherungstechnische bzw. juristische Entscheidungen zur Schadensregulierung.
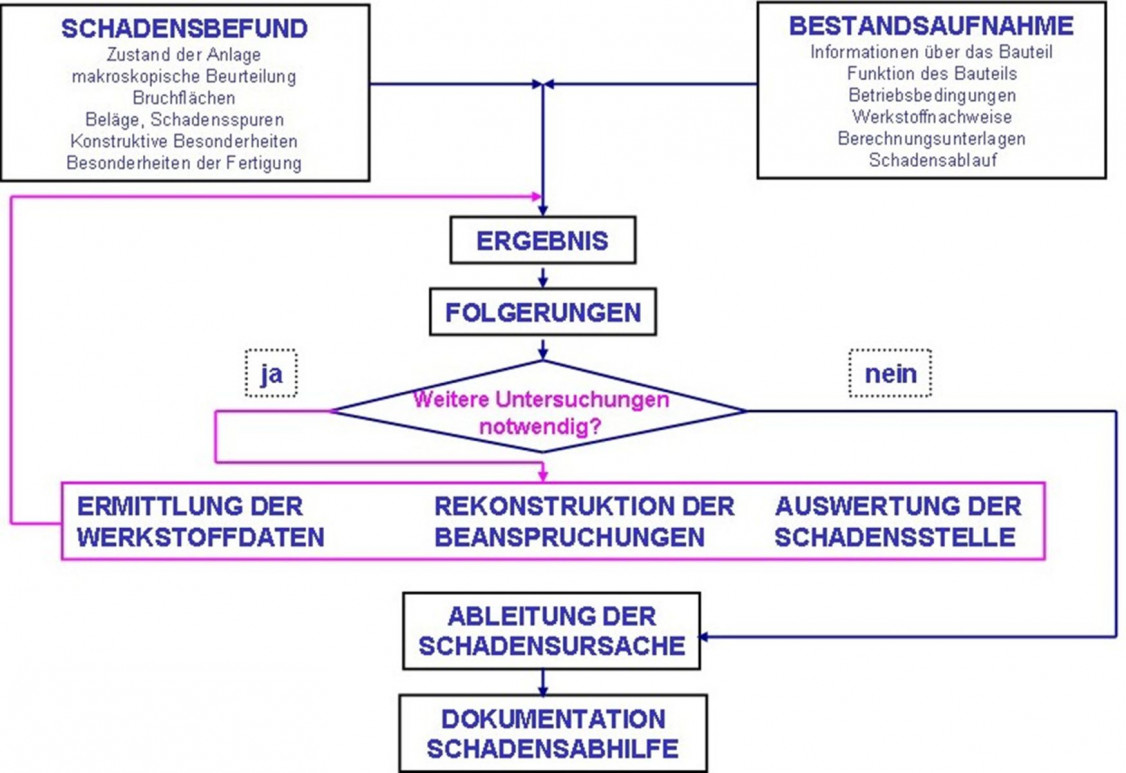
Hersteller und Betreiber profitieren
Solange die Schadensursache nicht eindeutig geklärt ist, vertreten sowohl der herstellende Betrieb als auch der geschädigte Betreiber häufig die Position, dass sie selbst keine Schuld an dem Schaden tragen, sondern die Ursachen bei Fehlern des anderen liegen. Vor einer schweißtechnischen Reparatur sollten möglichst viele Informationen über das zu Schaden gekommene geschweißte Bauteil und den Schadensablauf eingeholt werden, um die Schadensursachen objektiv aufzudecken.
Die Schadensursache entscheidet, ob und wie eine schweißtechnische Instandsetzung erfolgen sollte, um einen dauerhaften Weiterbetrieb der Anlage oder des Bauteils zu gewährleisten, und wer die Kosten für Produktionsausfall, Reparatur oder Ersatzleistungen trägt; für wen also die Schadensfallanalyse „zum Segen oder zum Fluch“ wird.
Eine objektive Schadensanalyse führt zur Aufklärung des vorliegenden Schadensfalls und eventuell zu fallbezogenen Verbesserungsmaßnahmen. Davon profitieren sowohl Hersteller als auch Betreiber. Für den Schweißbetrieb erweitern sich die Erfahrungen zur beanspruchungsund fertigungsgerechten Bauteilgestaltung und -herstellung. Aber auch der Betreiber profitiert nicht nur von der technischen Optimierung der Bauteile oder Anlagenkomponenten, sondern auch von erforderlichen Maßnahmen zur Verbesserung des Betriebs bzw. der funktionsgerechten Fahrweise der Anlagen.
(Autor: Prof. Dr.-Ing. Norbert Woywode, Ingenieurbüro E & C Woywode, Büro Magdeburg, norbert.woywode@t-online.de)
Literatur:
[1] Woywode, N.: Schäden an Schweißkonstruktionen vermeiden. In: Jahrbuch Schweißtechnik 2010, S. 136–144. DVS Media, Düsseldorf 2009.
[2] Woywode, N.: Vertrauen ist gut, Kontrolle ist besser – Beispiele aus der Schweißtechnik. In: Jahrbuch Schweißtechnik 2016, S. 292–297. DVS Media, Düsseldorf 2015.
[3] Herold, H.; Pieschel, J.; Woywode, N.: Fertigungsbedingte Risse durch ungünstige schweißtechnische Gestaltung und Ausführung. Zeitschrift für Metallkunde 92 (2001), Nr. 3, S. 232–236.
[4] Dombrowski, J. (Hrsg.): Schweißschäden: Ursachen – Bewertung – Vermeidung. Charles Coleman Verlag, Köln 2019, S. 244–247.
[5] Schmitt-Thomas, K.: Integrierte Schadensanalyse: Technikgestaltung und das System des Versagens. 2., bearbeitete und erweiterte Auflage. Springer-Verlag, Berlin, Göttingen, Heidelberg 2005.
[6] Woywode, N.: Ermüdungssicher gestaltete Schweißkonstruktionen und Empfehlungen des Eurocode 3. 13. Schweißtechnische Fachtagung. SLV Halle GmbH, Halle/Saale 2003.
[7] Woywode, N.: Beanspruchungs- und fertigungsgerecht gestalten, Ursachen von Schadensfällen an Schweißkonstruktionen vermeiden. Fortbildung für SAP. SLV Halle GmbH, Halle/Saale 2014.
Schlagworte
DIN EN 1090DIN EN ISO 5817EXC 1EXC 4HeißrisseInstandsetzungKaltrisseLamellenrisseQualitätssicherungRelaxationsrisseSchadensfälleSchweißkonstruktionenSchweißtechnikWPS