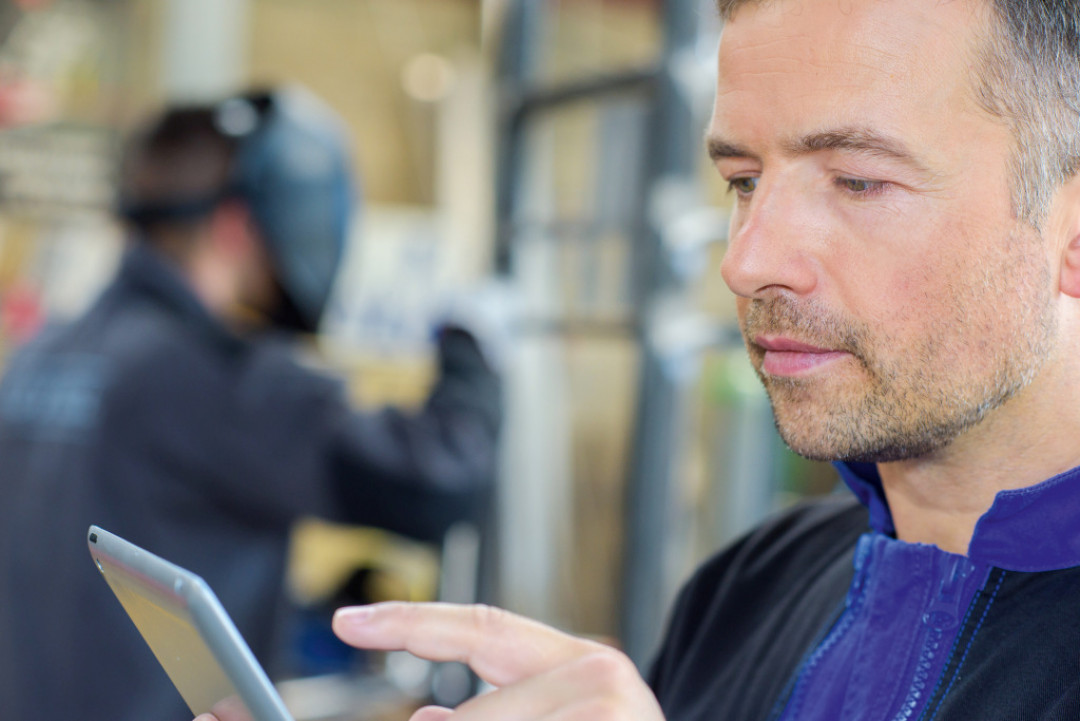
„Vom Fortschritt profitieren: Industrie 4.0 in der Schweißtechnik“
„Industrie 4.0“ ist für kleine und mittelständische Unternehmen (KMU), die sich mit dem Fügen, Trennen und Beschichten auskennen, künftig von großer Bedeutung. Dabei geht es aber weniger darum, konkrete Produktions-, Fertigungs- oder Schweißprozesse zu beschreiben, sondern kritisch zu prüfen, wo in kleinen und mittelständischen Unternehmen Lücken hinsichtlich Industrie 4.0 bestehen und wie sich diese schließen lassen. Denn nur so können die Unternehmen langfristig den bestehenden, digitalen Vorsprung für sich nutzen.
Aus diesem Grund beschäftigt sich die Arbeitsgruppe „Industrie 4.0“ im DVS aktuell mit diesem Thema. Sie stößt die Diskussion über die Digitalisierung in der Schweißtechnik an und initiiert unter dem Titel „Vom Fortschritt profitieren: Industrie 4.0 in der Schweißtechnik“ eine Serie von Fachbeiträgen, die – mit der vorliegenden Ausgabe beginnend – in dieser Zeitschrift veröffentlicht werden.
Jetzt zum Download
Parallel dazu ist aktuell ein DVS-Whitepaper mit dem Titel „Vom Fortschritt profitieren: Industrie 4.0 in der Schweißtechnik“ erschienen. Es bietet einen ersten Einstieg ins Thema, benennt Vorteile der Digitalisierung für die schweißtechnischen Betriebe und listet Anlaufstellen sowie Informationsplattformen auf. Das Dokument kann aus dem Internet heruntergeladen werden:
Schweißtechnik 4.0: Digitalisierte vernetzte schweißtechnische Fertigung – Konzepte und Anwendungen (Teil 2)
4. Vertikale Integration: Vom Schmelzbad zum „Top Floor“
In Kapitel 2 wurden netzwerkfähige digitalisierte Schweißstromquellen und Datenmanagementsysteme als Voraussetzung für Schweißtechnik 4.0 genannt. Ferner wurde darauf hingewiesen, dass darüber hinaus alle „Elemente“ der schweißtechnischen Fertigung, das heißt Anlagen, Bauteile und das schweißtechnische Personal, durchgängig digital vernetzt werden können. Dadurch sind diese Elemente der schweißtechnischen Fertigung mit den Führungssystemen des anwendenden Unternehmens kommunikationsfähig. Dies wiederum ermöglicht eine vertikale Integration über alle Ebenen der „Automatisierungspyramide“ hinweg, wobei die Bauteile ausdrücklich einbezogen werden (vergleiche dazu unter anderem [5; 6; 23; 24]).
Im Kontext von Schweißtechnik 4.0 reicht die vertikale Integration somit „vom Schmelzbad bis zum Top Floor“, das heißt vom Bauteil in die Führungssysteme des Unternehmens. Voraussetzung dafür ist das im Kapitel 3 beschriebene „cloud-basierte Datenmanagement“.
Bild 2 zeigt dazu auf der linken Seite die klassische hierarchisch aufgebaute Automatisierungspyramide und auf der rechten Seite deren „Auflösung“ mit cloudbasierten Führungssystemen und einer dezentralen Prozesssteuerung mittels smarter Elemente der schweißtechnischen Fertigung. Neben einer smarten Stromquelle sind beispielsweise auch Schweißbrenner, Drahtkoffer, Steuereinheit und Roboter genannt. Auch das Werkstück wird als ein smartes Element der schweißtechnischen Fertigung betrachtet. Hinzu kommt „der Schweißer“ als Vertreter des bereits genannten smarten schweißtechnischen Fachpersonals.
![Bild 2: Vertikale Integration in der schweißtechnischen Fertigung [2...4]. Bild 2: Vertikale Integration in der schweißtechnischen Fertigung [2...4].](/storage/media/images/7167/conversions/bild-2-full.jpg)
Mit einer solchen vertikalen Integration sind nun grundsätzlich Funktionen und Vorteile der Vernetzung nutzbar. Zwei wesentliche sind
- die umfassende, echtzeitnahe Visualisierung aller Abläufe und Ressourcen für die (schweißtechnische) Fertigung im Unternehmen (zum Beispiel für die Betriebs- und Unternehmensführung des Anwenders) und
- das Reporting und die Dokumentation (als Dienstleistung für den Kunden des Anwenders). Dies umfasst auch den Austausch von Auftrags- und Qualitätsdaten, die Überwachung von Verbrauchsmaterial und die Rückmeldung von Arbeitsergebnissen in Form von Qualitätsberichten.
Eine vertikale Integration ermöglicht weiterhin die folgenden Anwendungen:
- vorausschauende Prozesse für Wartung und Instandhaltung von Maschinen und Anlagen beim Anwender und
- schnelle (echtzeitnahe) Fehlerdiagnose und Fehlerbehebung (auch erweiterbar um die Funktionserweiterung der Anlage durch Software-Updates).
Dadurch, dass nun die ersten Elemente einer solchen vernetzten schweißtechnischen Fertigung zur Verfügung stehen und angewandt werden, gelingt ein Einstieg in die Umsetzung von Industrie 4.0 für das Metall-Schutzgasschweißen.
5. Vernetzte Produktgüte beim Metall-Schutzgasschweißen (in Anlehnung an [3; 4])
Dieser Einstieg erfolgt anhand einer Betrachtung der Produktgüte in der schweißtechnischen Fertigung. Dazu stellt das folgende Konzept das Endergebnis einer jeden fügetechnischen Fertigung in den Mittelpunkt: die Produktgüte, Bild 3.
![Bild 3: Vernetzte Produktgüte in der schweißtechnischen Fertigung [3; 4]. Bild 3: Vernetzte Produktgüte in der schweißtechnischen Fertigung [3; 4].](/storage/media/images/7168/conversions/bild-3-full.jpg)
Das Konzept basiert auf der Vernetzung von Informationsquellen, die über Modellbildung, Statistik und Empirie zusammengeführt und interpretiert werden können. Die entsprechenden Modelle können dabei zum Beispiel aus bekannten physikalischen Zusammenhängen abgeleitet oder mittels „Machine Learning“ (vergleiche Kapitel 3.2) angelernt werden.
Zwar bietet die bisherige automatisierte schweißtechnische Fertigung aufgrund ihrer häufig schon fortgeschrittenen digitalisierten Komponenten gute Voraussetzungen für die Umsetzung von Industrie 4.0, die Schweißtechnik wird jedoch aufgrund ihrer Komplexität auch weiterhin von erfahrenem und gut ausgebildetem schweißtechnischem Personal leben, deren Arbeit durch vernetzte Produktionslösungen allerdings vereinfacht und verbessert werden kann. Der Schweißprozess selbst, und insbesondere das hier betrachtete Metall-Schutzgasschweißverfahren, hängt von einer Vielzahl wechselwirkender Einflüsse ab, die wiederum die resultierende Produktgüte bestimmen. Als Beispiele seien hier die Beschaffenheit des Schweißzusatzwerkstoffs, die gewählte Lichtbogenart oder die Schweißposition genannt.
Erfahrenes schweißtechnisches Personal kann die entscheidenden Wechselwirkungen einschätzen und bei Bedarf gegensteuern, um die resultierende Produktgüte abzuschätzen und zu gewährleisten. Häufig allerdings können unerwartete Änderungen von Randbedingungen oder Informationen, die der menschlichen Wahrnehmung verschlossen bleiben, nur schwerlich ausgeglichen werden. Gelingt es somit, Informationsquellen zu den verschiedenen Einflussgrößen zu vernetzen, diese dem schweißtechnischen Personal oder den datenverarbeitenden Strukturen bereitzustellen, können damit gesamtheitliche Aussagen über den Prozesszustand und letztendlich über die Produktgüte getroffen werden.
Diese Informationsquellen können nach Bild 3 den am Schweißprozess beteiligten Komponenten (Drahtantriebsrolle, Stromkontaktrohr, ...), den Prozessdaten (Schweißspannung, Schweißstrom, ...) und den Randbedingungen (Werkstück, …) zugeordnet werden. Zu den vernetzten Quellen können dabei Daten ihren Eigenschaften zugeordnet werden, die Einfluss auf die Produktgüte nehmen können.
Liegen Daten zu den zuvor beschriebenen Quellen vor, können sie über modellbildende, statistische und empirische Verfahren zusammengeführt und interpretiert werden. Aufgrund dieser Informationen lässt sich somit die Historie und Prädiktion des Schweißprozesszustands ableiten. Ein unregelmäßiger Prozesszustand, der zum Beispiel zunächst durch schwankende Kurzschlussfrequenzen in den Prozessdaten sichtbar wird, kann auf falsche oder verschlissene Drahtantriebsrollen zurückgeführt werden. Sind darüber hinaus die Grenzen der zulässigen Prozesszustände je nach Anwendung bekannt, lässt sich wiederum die erzielte Produktgüte ableiten.
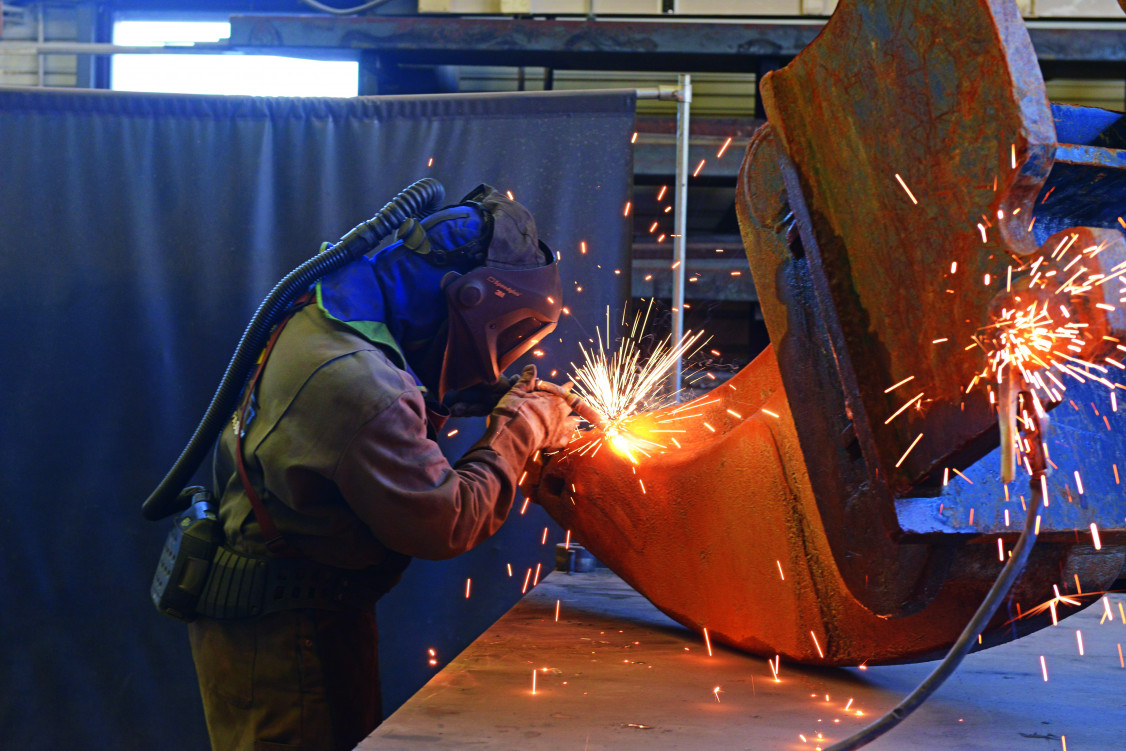
Einfache Informationen zum Beispiel zur verwendeten Drahtrolle können schnell und intuitiv erfasst werden, andere Informationen wie die genaue Anzahl an Betriebsstunden der Einzelkomponenten können vom schweißtechnischen Personal weniger gut erfasst werden. Der beschriebene Prozesszustand ersetzt somit nicht das Fachwissen des schweißtechnischen Personals, sondern ergänzt es und eröffnet den Zugang zu Zusammenhängen, die bisher verschlossen waren.
Ferner bestätigt sich dadurch noch einmal, dass die Auswirkungen einer Schweißtechnik 4.0 auf das schweißtechnische Personal auf allen Ebenen zu betrachten sind. Informationen müssen über alle beteiligten Parteien sicher und in zulässigen Zeiträumen erfasst, verarbeitet und zur Verfügung gestellt werden. Dies ist eine der wesentlichen Voraussetzungen einer Schweißtechnik 4.0. Das vorgestellte Konzept stellt damit eine interessante Anwendung der vernetzten, digitalisierten schweißtechnischen Fertigung dar. Zu Anwendung und Erprobung dieses Konzepts unter dem Begriff Applikationsregelung siehe [25; 26].
6. Ausblick: Handlungsrahmen für Schweißtechnik 4.0
Die bisher genannten Grundlagen und Anwendungen stellen nur einen ersten Schritt in Richtung Umsetzung von Schweißtechnik 4.0 dar. In [1] wird für die nächste Zukunft von einer „anspruchsvollen Lernphase“ gesprochen, in der sich die Schweißtechnik trotz aller Fachkenntnis und trotz aller Kenntnisse über die Digitalisierung befindet. Es wird eine gemeinsame, konzertierte Vorgehensweise erforderlich sein, an der unter anderem Hersteller und Lieferanten von schweißtechnischen Anlagen, Werkstoffen, Zusatzwerkstoffen und Hilfsstoffen beteiligt sein müssen, ferner aber auch Hersteller und Lieferanten von Automatisierungstechnik sowie Anbieter von Hard- und Software. Unerlässlich ist auch die aktive Beteiligung von Fachleuten aus den Bereichen Qualitätssicherung, Normung sowie Aus- und Weiterbildung.
Festzuhalten bleibt, dass die Einbeziehung der hier genannten Akteure mit der Nutzung einer Vielzahl von Daten unterschiedlicher Herkunft und Qualität verbunden sein wird. Eine vernetzte schweißtechnische Fertigung wird dazu ein Datenmanagement (siehe Kapitel 3.2) betreiben, welches nicht nur Daten aus dem Schweißprozess und aus den vor- und nachgeschalteten Prozessen zusammenführt. Vielmehr werden auch Daten aus der „Supply Chain“ und aus der Nutzung der geschweißten Produkte zusammengeführt werden müssen. Untersuchungen in [27] sprechen von einer „allgegenwärtigen Nutzung von Daten“ (ubiquitous utilization of data).
Aus der genannten Lernphase und aus der weiteren Zusammenarbeit von Akteuren der Schweißtechnik sind weitere Veröffentlichungen zum Thema Schweißtechnik 4.0 zu erwarten. Diese Veröffentlichungen können sich an dem in Bild 4 beschriebenen Handlungsrahmen orientieren. Dieser Handlungsrahmen stellt das Bauteil und die Bauteilqualität in den Mittelpunkt. Dazu werden Elemente der schweißtechnischen Fertigung skizziert, die einen Einfluss auf das Bauteil und auf die Bauteilqualität haben.
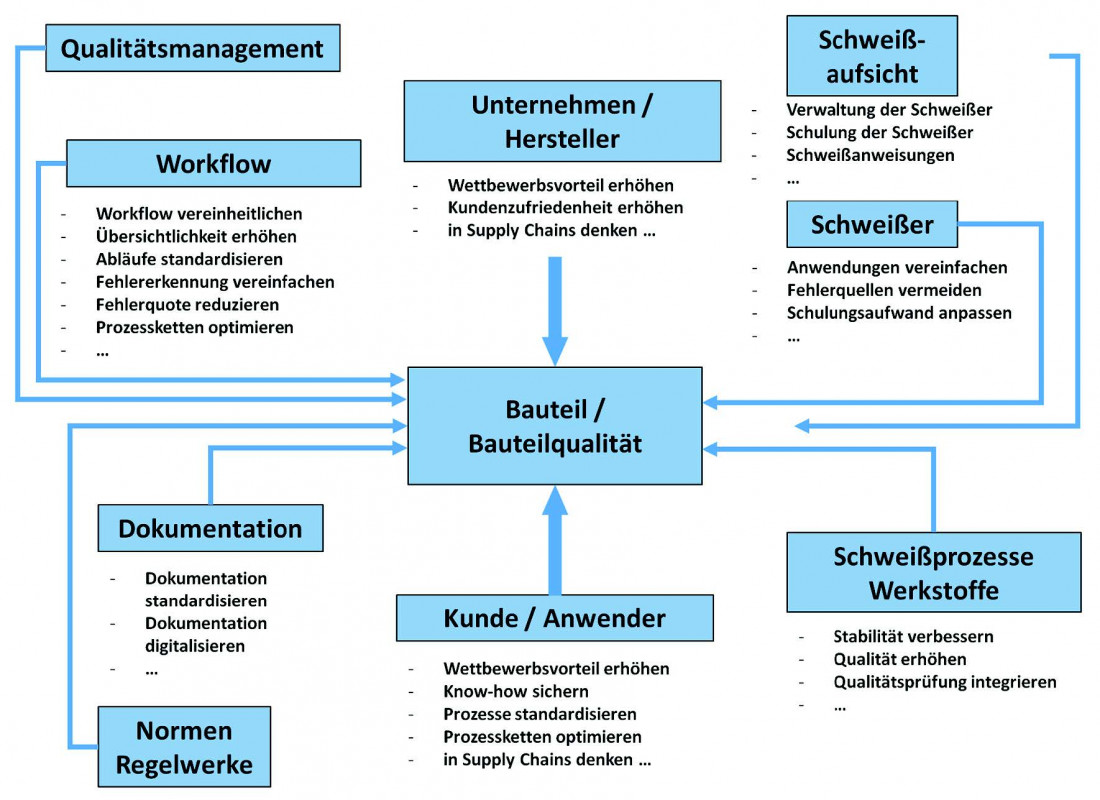
In weiteren Veröffentlichungen kann eine Übertragung der Erkenntnisse auf verschiedene Werkstoffe und auf verschiedene Schweißprozesse mit ihren jeweiligen Randbedingungen erfolgen. Von hoher Bedeutung ist dabei die Einbeziehung aller Elemente der Qualitätssicherung und der digitalen Qualitätsprüfung. Einen wichtigen Schwerpunkt in der Anwendung von Schweißtechnik 4.0 stellt die aktive Einbindung des schweißtechnischen Personals dar. Im Handlungsrahmen für Schweißtechnik 4.0 müssen dazu überzeugende Konzepte entwickelt werden.
(Autoren: K. Middeldorf, Hochschule für Oekonomie und Management, Köln, D. Aumüller, J.-P. Bergmann, TU Ilmenau, S. Mann, R. Sharma und U. Reisgen, RWTH Aachen University)
Literatur
[1] Gunzelmann, K.-H., u. a.: Vision zur Digitalisierung der Schweißtechnik hin zu Industrie 4.0. Schw. Schn. 72 (2020), H. 9, S. 566/73.
[2] Middeldorf, K.: Schweißtechnische Fertigung – Ready for „Industrie 4.0“. Der Praktiker 70 (2018), H. 1–2, S. 34/41.
[3] Reisgen, U., u. a: Connected, digitalized welding production – Industrie 4.0 in gas metal arc welding. Wdg. in the World 63 (2019), H. 4, S. 1121/31.
[4] Reisgen, U., u. a.: Vernetzte, digitalisierte, schweißtechnische Fertigung – Industrie 4.0 beim Metallschutzgasschweißen. DVS-Berichte Bd. 344, S. 181/93. DVS-Media, Düsseldorf 2018.
[5] Bauernhansl, T., u. a.: WGP-Standpunkt Industrie 4.0. WGP – Wissenschaftliche Gesellschaft für Produktionstechnik 2016.
[6] Gorecky, D., u. a.: Wandelbare modulare Automatisierungssysteme. In: Reinhart, G., „Handbuch Industrie 4.0“, S. 555/86. Carl-Hanser-Verlag München 2017.
[23] Siepmann, D.: Industrie 4.0 – Fünf zentrale Paradigmen. In: Roth, A. „Einführung und Umsetzung von Industrie 4.0“, S. 35/72. Springer-Gabler-Verlag, Wiesbaden 2016.
[24] Bauernhansl, T.: Industrie 4.0 – Im Spannungsfeld von Markt, Technik und Organisation. Organisationsentwicklung (2017), H. 2, S. 32/38.
[25] Reisgen, U., u. a.: GMAW in the internet of production. Wdg. J. 99 (2020), H. 11, S. 38/42.
[26] Reisgen, U., u. a.: Study on weld seam geometry control for connected gas metal arc welding systems. Vortragsbd. 17. Int. Conf. on Ubiquitous Robots 2020, S. 373/79. Institute of Electrical and Electronics Engineers (IEEE ) 2020.
[27] Mann, S., u. a.: Connected, digitalized welding production – Secure, ubiquitous utilization of data across process layers. Advanced Joining Processes (2020), S. 101/18. DOI: 10.1007/978-981-15-2957-3_8.
Schlagworte
DigitalisierungFachpersonalFertigungFügetechnikIndustrie 4.0IoTKMUManuelles SchweißenSchweißenSchweißtechnik