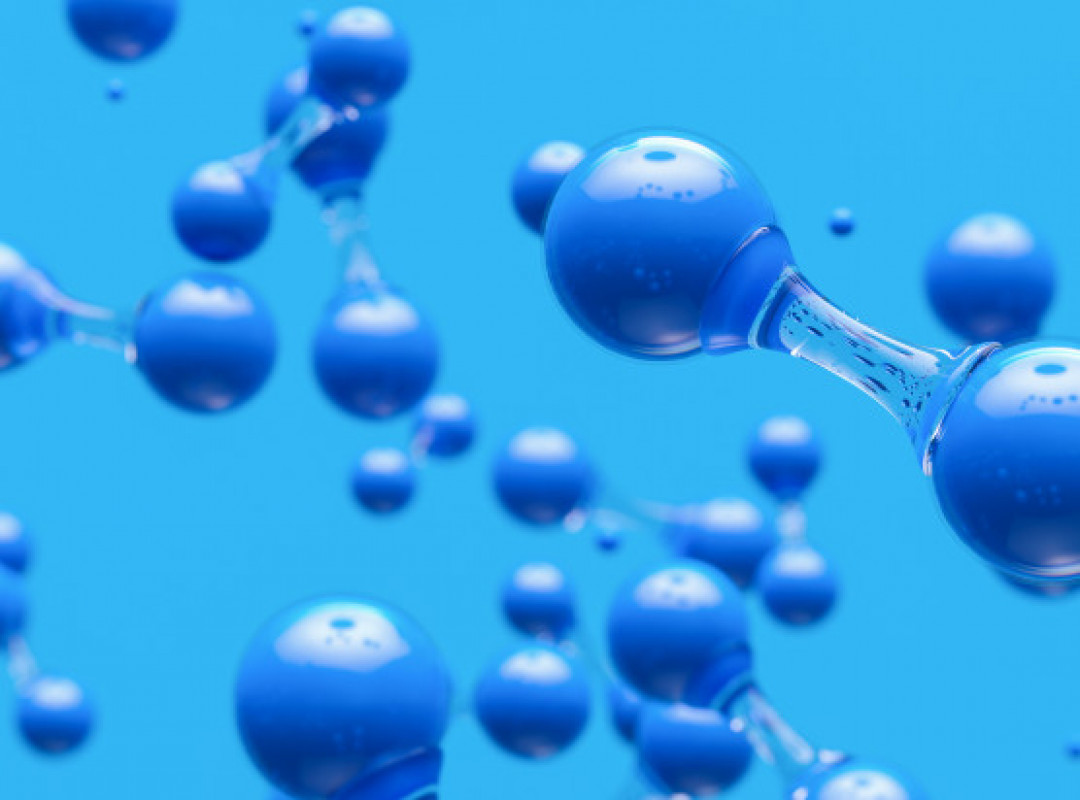
"We need to remain open to technology."
Prof. Dr.-Ing. Emil Schubert – known as WELDPROF® – is not only a professor of joining technology and received his PhD in materials science but is also the managing director of Alexander Binzel Schweisstechnik GmbH & Co. KG. In this interview, he provides insights into the topic of hydrogen: its applications, how to avoid hydrogen in welding, and the prospects it offers in the hydrogen economy.
What role does hydrogen play in joining technology concerning weld seams?
Schubert: Hydrogen is a gas characterized by a very small atomic size. Such a small atom initially fits anywhere. While welding doesn't necessarily operate on the atomic level, it eventually does. When I weld and hydrogen enters my weld material, it tends to escape. If it stays inside, it strives to recombine. The atomic gas components coagulate and form pores. If I have pores in my weld seam, there's a cross-sectional weakening. My component no longer meets the requirements. Hydrogen usually enters the weld material through inadequate preparation. For example, if I haven't properly cleaned my sheets or components, or if there's moisture on them. This is particularly critical with aluminium. Hydrogen's solubility in liquid aluminium is very high; its solubility in solid aluminium is very low. As the aluminium solidifies, hydrogen wants to escape. If I don't give it enough time to escape and outgas, pores form. But hydrogen can enter my weld seam in many other ways — through moisture in the base material, through the wire if it's not stored dry, and so on. This can lead to pores just as critically as with aluminium components. It's especially concerning when transporting hydrogen in a steel pipe. If I have pores at the connection point there, the hydrogen intended to be transported through that pipe will naturally escape through these pores. The key is always the component pre-treatment, proper cleaning, and the storage of filler wires.
Is automation a lever for better control?
At least the process is more controlled. I can also better plan my welding parameters if I know precisely that my sheet has been stored for so long, and maybe there's a hydroxide layer on it. But this layer is consistently thick if I store it for the same duration each time before the welding process. My welding parameters are always constant, and I can set them up so that, for example, the outgassing of hydrogen can take place. Then I know I'm not welding too quickly. If I weld too quickly, hydrogen doesn't have the opportunity to escape from the liquid weld material in time. This can be easier to adjust when welding automatically compared to manual welding, where the welder may be under pressure to complete the task as quickly as possible.
Where does hydrogen come into play in the hydrogen economy?
Currently, the burning issue is the climate crisis. We are facing global warming mainly caused using fossil fuels. We need to move away from that. Hydrogen is a non-fossil fuel. That's the main point! Unfortunately, unlike other gases, hydrogen is almost absent in the air. It must be produced. To generate hydrogen, I need electricity. Ultimately, it is primarily obtained from water, H2O. I need to split the water into H2 and O2. The energy I need for this is primarily electrical power. But if I generate my electrical power from fossil fuels, I haven't gained anything. Then we're not talking about green hydrogen. Green hydrogen, by definition, is hydrogen produced from renewable energies. That means I need to focus on the step before hydrogen production. I need green power. With green power, I can produce green hydrogen.
If I need electricity to produce hydrogen but just want to replace my electricity, isn't that redundant?
What is often forgotten is that hydrogen is an ideal energy storage medium. I can't store electricity arbitrarily. I generate it, then it is transported through our overhead lines or buried in the ground. But I can't store it very well. I can transport hydrogen somewhere, then store it temporarily, and finally use it where I need it. In the end, I convert it back into electricity, of course. This can be done, for example, with a fuel cell or a gas burner. There are more conversions, but ultimately, there is the possibility of storage.
Do you believe it will be possible to operate welding equipment with hydrogen?
We still have a certain percentage of autogenous welding and cutting technology. But most of what we do is arc welding. And to generate an arc, I need electrical power, usually direct current. Our outlets provide alternating current, which needs to be converted back to direct current for welding. Now, I could build a battery power source. Those exist today. In the future, I could theoretically have a small fuel cell that supplies energy to my welding equipment. Therefore, it's conceivable, but we're not there yet today.
Is that economically viable or will become so?
In my opinion, it can become viable. Today, I also have losses when converting alternating current from my network into welding current. Even a welding inverter has an efficiency of 85 to 90 percent. That means I also have losses. If I generate direct current from a fuel cell in the future, I probably have losses of a similar magnitude. Now, the hydrogen networks in Germany are not yet developed to a level that enables the actual use of green hydrogen. Currently, it's more grey hydrogen. Plus, the supply is not guaranteed. Most of the green hydrogen circulating must be purchased.
If sustainability is important, you naturally want to use green hydrogen. What still needs to be done politically to achieve this?
Ultimately, both efforts must happen concurrently. We need more green electricity—expanding wind power, solar, and hydropower. This is in progress but needs to be accelerated. If implemented consistently, there will be enough green electricity to generate green hydrogen. But currently, we don't have the capacity. We need larger electrolysers. This is where joining technology comes into play.
Can joining technology assist in making it available?
The core components of electrolysers are bipolar plates, which are often joined using laser welding. This is a significant application area. There are thousands, even tens of thousands of such bipolar plates in an electrolyser. Much larger production capacities need to be created. Additionally, the entire area of hydrogen supply and the routing of the generated gases opens up. This happens in pipeline systems. These pipes all need to be welded gas-tight. But since much higher quantities will be needed; this will have to be automated. This means pipe and pipe root welds, which are currently done manually, connections of individual gas lines, will need to be done in the future through automated orbital welding. A significant market for joining technology which has not yet been explored to its full extent .
A second aspect would be the use of hydrogen as an energy source?
Exactly. The question is where to store the hydrogen. Either I store it right after generation, or I transport it somewhere first and store it there. But eventually, I must store it. Most often, this is done in high-pressure storage. Ultimately, these are pressure vessels, and the demand will keep increasing. Many pressure vessels are manually welded today. This will have to be automated. If I want to weld very large pressure vessels, I will need very thick walls, i.e., multi-layer welding. Automated multi-layer welding is not necessarily standard everywhere. It's just emerging. If I need such multi-layer welding, for example, with a total of 30 layers, I must use sensors to see where the next seam should be positioned. Especially automated multi-layer welding is certainly still a challenge. Much manual welding is still done today, and you won't get much further with larger volumes.
Are you as a company also working on automating these multi-layer welding processes in research and development?
Yes, we are working with a partner to be able to determine the position of the next layer automatically. We see a need for this both in pressure vessels and in the field of renewable energy generation. In the context of the climate strategy for 2035, it is always said that we need to switch to renewable energies. What the average citizen forgets is that a wind turbine doesn't build itself. It requires steel and joining technology. For the transport of hydrogen, pipelines are needed, which are currently not sufficiently available. Of course, in the existing natural gas network, up to 70 percent hydrogen can be mixed and used. Higher hydrogen content becomes critical because hydrogen may escape at the joints. If I want to deliver hydrogen everywhere comprehensively, we currently need between 3,000 and 10,000 kilometres of additional pipelines in Germany alone. Again, welding will be required. Probably more than half of all pipelines are manually welded today. With this quantity, it will have to be further automated.
We've talked about generation, storage, and transport. What about utilization?
There are two possibilities: one is the fuel cell, with which I can generate electricity. There are intensive laser welding applications in use that are like electrolysers with respect to fuel cells. The second option is gas burners. Here, I can burn hydrogen, for example, along with natural gas and oxygen in a controlled manner to generate energy. A lso for heating: industrial heaters, residential heaters—anywhere I replace the current oil or gas burner with a hydrogen burner. Fuel cells are in demand in the field of mobility. A lot is happening there. Perhaps less so in the automotive sector, where battery technology is primarily used. But this is all just the beginning. Here again, there's the issue of scaling.
Will there be a need for expanding the hydrogen network in Germany in the future?
In the future, we want to source green hydrogen not from abroad but from Germany. Ultimately, it is nonsense to produce hydrogen from fossil energy sources. And we need to remain open to technology. It is a mistake to say that everything must now be based on battery technology. Perhaps the fuel cell is an alternative in some areas, maybe even e-fuels. Ultimately, the goal is to make the technology environmentally friendly and not to push it. That would be my wish: sensible information policy; not promoting ideologies but really providing technical solutions which are clearly based on facts.
Thank you for the conversation.