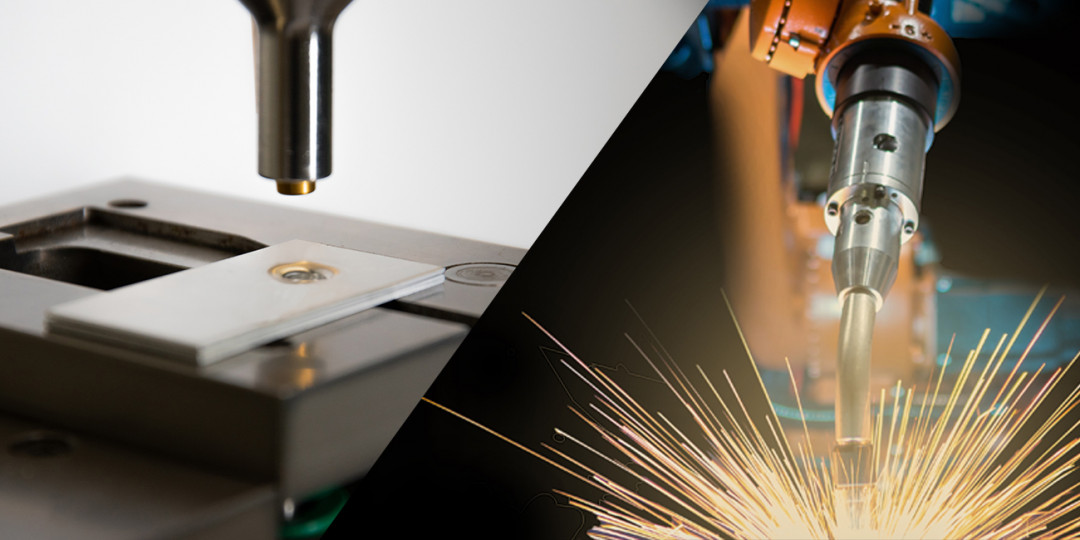
Um die Vorteile bei der Energieeffizienz zu belegen, hat TOX PRESSOTECHNIK das Laboratorium für Werkstoff- und Fügetechnik der Uni Paderborn beauftragt, eine Energieverbrauchsmessung für das Widerstands-Punktschweißen durchzuführen. Das Institut untersuchte eine artreine Stahl- und eine artreine Aluminium-Verbindung.
Gewinner in Sachen Energie
Das Ergebnis: Das Clinchen hat bei beiden Materialkombinationen die Nase vorn. Es lassen sich je nach Fügeverbindung im Vergleich zwischen 80 und 90 Prozent Energie einsparen. „Sie reduzieren ihren CO2-Fußabdruck also deutlich, wenn sie clinchen statt schweißen. Zumal beim Clinchen ein zusätzlicher Energieverbrauch durch Lüften oder Absaugen komplett entfällt“, betont Dr. Marcus Matzke.
Das Verfahren punktet aber nicht nur beim Energieverbrauch. Die Unternehmen sparen auch noch an anderer Stelle: Da eine Clinchverbindung allein durch die Umformung der Fügeteile hergestellt wird, sind keine Hilfsfügeteile wie Schrauben, Mutter oder Nieten notwendig. Auch das Investment für eine etwaige Zuführeinrichtung entfällt damit. Es müssen weder Kühlmittel oder Gas zugeführt werden, noch fallen Chemikalien und sonstige Schadstoffe zur Entsorgung an. Außerdem entstehen beim Clinchen keine giftigen Dämpfe, die dem Bedienpersonal schaden könnten. Und der Geräuschpegel im Betrieb ist deutlich niedriger. „Was den finanziellen Aufwand angeht, rechnen wir im direkten Vergleich mit 40 Prozent geringeren Investitions-, Betriebs- und Werkzeugkosten für unsere Kunden“, fasst der Technologieleiter zusammen.
(Quelle: Presseinformation der TOX PRESSOTECHNIK GmbH & Co. KG)
Schlagworte
ClinchenFügetechnikSchweißenSchweißtechnikWiderstandspunktschweißen